Table of Contents
Law of gearing
The Law of Gearing is a fundamental principle of mechanical engineering that relates to the relationship between the size of two gears in a gear train. It is a mathematical formula that determines the ratio between the number of teeth on two gears and how they interact with one another.
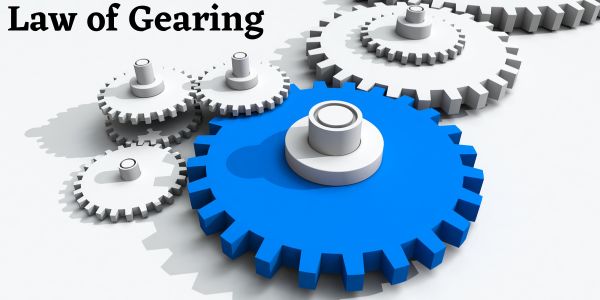
What is the Law of Gearing?
The Law of Gearing states that “The speed of two gears in a gear train is inversely proportional to their respective diameters”. In other words, the larger the diameter of a gear, the slower it rotates compared to a smaller gear. This is because a larger gear has more teeth than a smaller gear, and therefore it takes longer for each tooth to engage with its counterpart on the other gear.
The Law of Gearing can be expressed mathematically as follows:
N₁ / N₂ = D₂ / D₁
Where:
N₁ = number of teeth on the smaller gear
N₂ = number of teeth on the larger gear
D₁ = diameter of the smaller gear
D₂ = diameter of the larger gear
This formula shows that the ratio of the number of teeth on the two gears is equal to the ratio of their respective diameters. Therefore, if the number of teeth on one gear is known, the number of teeth on the other gear can be calculated using this formula.
The law of gearing derivation with respect to teeth and diameter
The key concepts and equations related to gear geometry and kinematics, are essential to understanding the law of gearing.
Gear Geometry and Kinematics:
It’s essential to understand the basics of gear geometry and kinematics. Gear geometry refers to the shape and size of the gear teeth and their arrangement on the gear circumference. The most common type of gear is spur gear, which has straight teeth and a cylindrical shape. The number of teeth on a gear is one of the critical parameters that determine its size and function. The diameter of a gear is also an essential parameter that affects the gear’s rotational speed and torque.
The kinematics of gears deals with the motion and forces that arise when two or more gears interact. When two gears mesh, the teeth on one gear engage with the teeth on the other gear, causing a rotational motion. The rotational motion of the two gears is related to their diameter and the number of teeth. This relationship is described by the law of gearing.
Law of Gearing Derivation:
The law of gearing relates to the rotational speeds and torques of two meshed gears. It is based on the concept of pitch circle diameter (PCD), which is the diameter of the imaginary circle that passes through the points where the teeth of the two gears touch. The PCD is a critical parameter in gear design as it determines the gear ratio, which is the ratio of the rotational speeds of the two gears.
The law of gearing can be derived using the principle of conservation of angular momentum. Angular momentum is a measure of the amount of rotational motion possessed by an object. When two gears are meshed, the angular momentum of one gear is transferred to the other gear, causing it to rotate.
Let’s consider two meshed gears, A and B, with PCDs of dA and dB, respectively. The number of teeth on gears A and B is NA and NB, respectively. The rotational speed of gear A is ωA, and the rotational speed of gear B is ωB. The torque on gear A is TA, and the torque on gear B is TB.
From the principle of conservation of angular momentum, we know that the angular momentum of the two gears must be equal. Therefore, we can write:
IA ωA = IB ωB
where IA and IB are the moments of inertia of gears A and B, respectively. We assume that the gears have the same density and material, so their moments of inertia are proportional to their masses and diameters.
We can also write the relationship between the torque and rotational speed of a gear using the equation:
T = I α
where α is the angular acceleration of the gear. If we assume that the angular acceleration is constant, we can write:
Δω = α Δt
where Δω is the change in rotational speed over a small time interval Δt.
Substituting these equations into the conservation of angular momentum equation and rearranging, we get:
TA dA = TB dB
Dividing both sides by dA dB and rearranging, we get:
ωB/ωA = dA/dB = NB/NA
This equation shows that the gear ratio, which is the ratio of the rotational speeds of the two gears, is equal to the ratio of their pitch circle diameters
Applications of the Law of Gearing
The Law of Gearing is used in a wide range of mechanical systems, from simple machines such as bicycles to complex machinery in manufacturing plants. Some common applications of the Law of Gearing include:
1. Gear trains in automobiles – The Law of Gearing is used to design the transmission systems in cars, which use a series of gears to transfer power from the engine to the wheels. By choosing the right combination of gears, engineers can optimize the performance of the car for different driving conditions.
2. Industrial machinery – Gears are used in a variety of industrial machinery, from conveyor belts to cranes. By applying the Law of Gearing, engineers can design these systems to operate efficiently and safely.
3. Robotics – Gears are also used in robotics to transfer power between different parts of the robot. By understanding the Law of Gearing, engineers can design robots that are more precise and efficient.
How the Law of Gearing Works?
To understand how the Law of Gearing works, it is helpful to consider a simple example. Let’s say we have two gears, one with 20 teeth (gear A) and the other with 40 teeth (gear B). The diameter of gear A is 2 inches, and the diameter of gear B is 4 inches.
Using the Law of Gearing formula, we can calculate the speed ratio between the two gears:
N₁ / N₂ = D₂ / D₁
20 / 40 = 4 / 2
This shows that gear B rotates at half the speed of gear A. In other words, for every revolution of gear A, gear B completes half a revolution.
The Law of Gearing is also used to calculate the torque ratio between the two gears. Torque is the rotational force generated by a gear, and it is directly proportional to the number of teeth on the gear. Therefore, if we know the torque generated by one gear, we can use the Law of Gearing to calculate the torque generated by the other gear.
Solved Examples
Example 1:
A gear system has an input gear with 20 teeth and an output gear with 40 teeth. If the input speed is 500 revolutions per minute (RPM), what is the output speed?
Solution:
Using the law of gearing, we can calculate the output speed as follows:
Output Speed/Input Speed = Number of Teeth on Input Gear/Number of Teeth on Output Gear
Output Speed/500 = 20/40
Output Speed = (20/40) * 500
Output Speed = 250 RPM
Therefore, the output speed of the gear system is 250 RPM.
Example 2:
A gear system has an input gear with 15 teeth and an output gear with 75 teeth. If the input speed is 1000 RPM, what is the output speed?
Solution:
Using the law of gearing, we can calculate the output speed as follows:
Output Speed/Input Speed = Number of Teeth on Input Gear/Number of Teeth on Output Gear
Output Speed/1000 = 15/75
Output Speed = (15/75) * 1000
Output Speed = 200 RPM
Therefore, the output speed of the gear system is 200 RPM.
Example 3:
A gear system has an input gear with 24 teeth and an output gear with 12 teeth. If the input torque is 50 Nm, what is the output torque?
Solution:
Using the law of gearing, we can calculate the output torque as follows:
Output Torque/Input Torque = Number of Teeth on Input Gear/Number of Teeth on Output Gear
Output Torque/50 = 24/12
Output Torque = (24/12) * 50
Output Torque = 100 Nm
Therefore, the output torque of the gear system is 100 Nm.
Also, read young’s modulus of elasticity