Table of Contents
Knurling is a fascinating and versatile machining technique that has been used for centuries to add texture, grip, and aesthetics to various objects and components. Whether you’re a mechanical engineer, a DIY enthusiast, or just curious about the world of machining.
Parameter | Straight Knurling | Diagonal Knurling | Diamond Knurling |
---|---|---|---|
Appearance | Straight parallel lines | Slanted lines | Cross-hatch pattern |
Application | Handles and thumbscrews | General purposes | Tool handles, knobs |
Machine/tool used | Knurling tool | Knurling tool | Two knurling wheels |
Feed direction | Axial | Axial or radial | Axial |
Typical Pitch | Coarse, Medium, Fine | Coarse, Medium, Fine | Coarse, Medium, Fine |
Pressure | High | Medium to high | High |
Surface Finish | Good | Better than straight | Best among all types |
Advantages | Simple pattern | Better grip than straight | Best grip |
Fewer chances of errors | Aesthetically pleasing | Aesthetically pleasing | |
Disadvantages | Better grip than a straight | Can cause material distortion | Requires precise alignment |
What is Knurling?
a. Knurling Defined Knurling is a manufacturing process that involves impressing a pattern of straight or diagonal lines onto a cylindrical or round surface. This textured pattern, called a knurl, provides enhanced grip, facilitates rotational movement, and adds aesthetic value to the machined part.
b. A Brief History Knurling has a rich history dating back to the early days of metalworking. It was initially used to improve the grip of tools and weapons. Over time, it found applications in various industries, becoming an essential technique in manufacturing.
c. Modern Applications In the modern era, knurling is used in industries such as automotive, aerospace, electronics, and consumer goods to improve the functionality and appearance of products. It can be found on everything from hand tools and engine components to decorative bottle caps.
Types of Knurling
a. Linear Knurling Linear knurling produces straight, parallel lines on the workpiece. It’s commonly used to enhance grip and is often seen on hand tools like wrenches and pliers.
b. Diamond Knurling Diamond knurling creates a pattern of diagonal lines that intersect to form diamond shapes. This type of knurling is favored for decorative and aesthetic purposes.
c. Straight Knurling Straight knurling, as the name suggests, produces straight lines without any diagonals or angles. It’s used when a simple and clean pattern is desired.
d. Cross Knurling Cross knurling combines linear and straight knurling to create a more intricate pattern. It’s often used in applications where both grip and aesthetics are important.
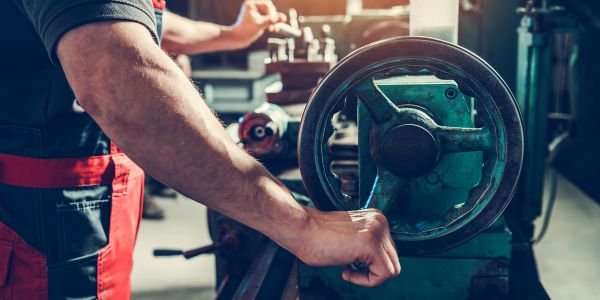
The Knurling Process
a. Tools and Equipment The knurling process requires a lathe equipped with a knurling tool. This tool consists of two knurling wheels with a pattern that matches the desired knurl. Lubrication and proper safety equipment are also essential.
b. Step-by-Step Procedure
- Mount the workpiece securely in the lathe.
- Position the knurling tool on the workpiece.
- Apply lubricant to reduce friction and heat generation.
- Engage the lathe and slowly feed the knurling tool into the workpiece.
- Repeat passes until the desired knurl depth and pattern are achieved.
c. Parameters to Consider
- Feed rate
- Depth of knurl
- Wheel diameter
- Lubrication
Applications of Knurling
a. Automotive Industry Knurling is used on various automotive components, such as steering wheel grips, gear shift knobs, and brake pedals, to improve driver control.
b. Aerospace Industry Aerospace engineers employ knurling to enhance the grip on control knobs, levers, and other critical components used in aircraft and spacecraft.
c. Consumer Goods In the world of consumer goods, knurling can be found on items like flashlights, pens, and kitchen appliances, where grip and aesthetics are crucial.
d. Medical Devices Knurling is used on medical instruments and devices to ensure healthcare professionals can maintain a secure grip during procedures.
The Science Behind Knurling
a. Material Properties The material being knurled must have the right hardness and ductility to avoid cracking or deformation during the process.
b. Friction and Grip The knurling pattern enhances grip by increasing the friction between the textured surface and the user’s hand or another object.
c. Heat Generation Friction generated during knurling can lead to heat buildup, which must be managed to prevent damage to the workpiece or tool.
d. Knurl Geometry The geometry of the knurl, including pitch, angle, and depth, directly affects the functionality and appearance of the finished product.
Challenges and Best Practices
a. Common Knurling Issues Common challenges in knurling include pattern inconsistency, tool wear, and workpiece deformation. These issues can often be mitigated through proper setup and maintenance.
b. Tips for Success
- Choose the appropriate knurling pattern and tool.
- Ensure proper lubrication.
- Monitor tool wear and replace as needed.
- Calibrate lathe settings accurately.
Knurling is a valuable machining technique that serves both functional and aesthetic purposes across a wide range of industries. Understanding the types, processes, and science behind knurling is essential for producing high-quality, textured surfaces that enhance grip, appearance, and overall product performance. Whether you’re an engineer, a machinist, or simply someone interested in the world of manufacturing, knurling is a skill worth exploring and mastering.
Also, read Sheet Metal Fabrication