Table of Contents
A more advanced version of the NC system is direct numerical control (DNC) machines where one computer controls multiple machines in real-time. The DNC system is not equipped with the tape reader and therefore increases the reliability of the machining system.
The prepared part program is transmitted from the computer’s memory directly to the machine tool. More than a hundred machines can be controlled at the same time by a single large computer system. The instructions needed for a given machine are provided on demand by the main computer.
For example, a machine that requires control commands will be immediately communicated to it by the computer. DNC systems are also equipped to collect the necessary data from machine tools.
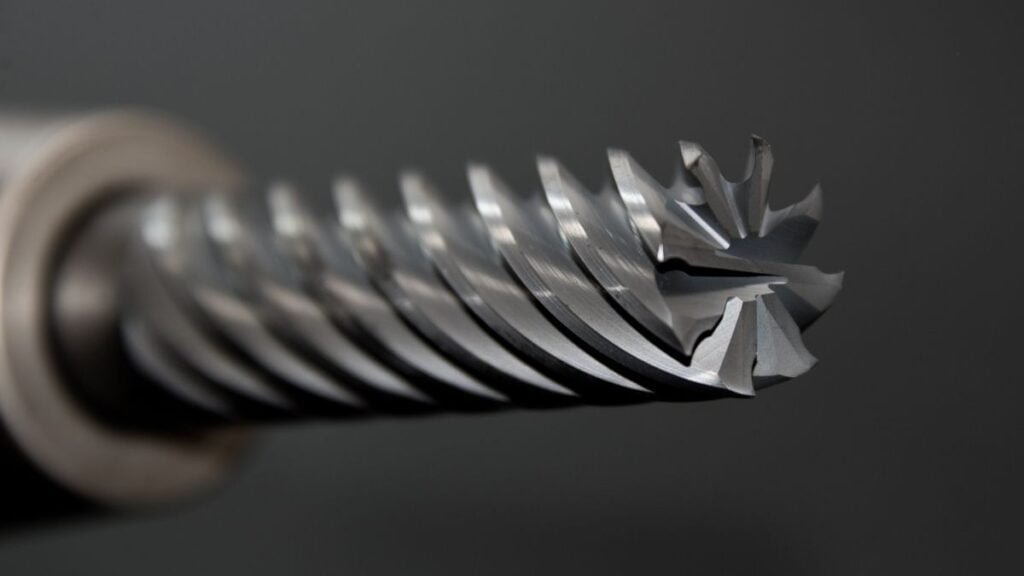
DNC Systems Components:
A “DNC system” stands for “Distributed Numerical Control” system also “Direct Numerical Control” system, which refers to a computerized manufacturing technology that controls and monitors machine tools in a production environment. It automates manufacturing processes and facilitates effective communication between a central computer and multiple machine tools. The system comprises several key components, which I will explain below:
- Central Computer: The central computer acts as the control hub of the DNC system. It operates specialized software that manages data flow and communicates with machine tools. The central computer receives part programs or instructions from the user and sends them to the relevant machine tools in the production line.
- Communication Network: The DNC system relies on a communication network to connect the central computer with the machine tools. This network can be wired (Ethernet, serial cables) or wireless (Wi-Fi), depending on the specific implementation. It enables the transfer of data, including part programs, tool data, and other instructions, between the central computer and the machine tools.
- Machine Tools: Machine tools are the physical equipment used for manufacturing operations, such as milling machines, lathes, drills, or grinders. In a DNC system, these machine tools have controllers that can communicate with the central computer. The controllers receive instructions from the central computer and execute the machining operations accordingly.
- DNC Software: The DNC system relies on specialized software that runs on the central computer and the machine tool controllers. This software handles tasks such as file management, data transfer, and real-time monitoring of the production process. It also includes features like error detection, tool path optimization, and tool change management to ensure efficient and accurate machining operations.
- Part Programs: Part programs contain instructions that guide the machine tools in performing specific manufacturing operations. These programs are created using computer-aided design (CAD) or computer-aided manufacturing (CAM) software and stored in the central computer. The DNC system transfers the relevant part program to the corresponding machine tool for execution.
- Machine Tool Controllers: Machine tool controllers are devices that interface between the central computer and the machine tools. They receive instructions from the central computer and convert them into signals that control the movement, speed, and other parameters of the machine tools. The controllers also provide feedback to the central computer, enabling real-time monitoring and control of the manufacturing process.
- Monitoring and Feedback Systems: The DNC system incorporates monitoring and feedback mechanisms to ensure the smooth operation of the manufacturing process. Sensors and feedback devices installed on the machine tools provide information about tool status, machine conditions, and process variables. This data is transmitted back to the central computer for analysis, monitoring, and quality control purposes.
- Security and Authentication: With the increasing connectivity and integration of manufacturing systems, security, and authentication measures are essential in a DNC system. These measures may include user authentication protocols, data encryption, access control mechanisms, and network security measures to protect the integrity and confidentiality of the data being transferred within the system.
A DNC system combines hardware, software, and communication infrastructure to enable efficient control, coordination, and monitoring of multiple machine tools in a manufacturing environment. It streamlines production processes, enhances productivity, and provides real-time visibility into manufacturing operations.
DNC Functions:
DNC systems serve to perform a variety of functions. The functions performed by DNC systems are difficult to perform with both conventional NC and CNC systems. The main functions of the DNC system are NC without punched tape, storage for the parts program, data collection, processing and reporting, and communications to and from the machine tools.
NC Parts Program Storage:
Storing part programs is another important function of DNC systems. Subsystems for storing programs must be properly structured. Framework subsystems must be able to readily provide programs to machine tools. Subsystems must have the capability to accommodate new part programs, delete old programs, and modify existing part programs, if any.
The post-processing function of converting the CLIFILE format from the stored part program to the downloadable instructions for the machine tool must be accurately performed by the DNC system. The other functions that must be performed by the subsystems include processing and managing data, displaying programs, and manipulating data.
Data Collection, Processing, and Reporting:
One of the other important functions of the DNC system is to collect machine data and transfer it to the control unit. This helps in real-time monitoring of production in the factory. Data relating to the number of components produced, tool usage, machine tool utilization, and other data relating to the measuring characteristics of the machine shop are collected and processed by the DNC system. The processed data is then used by management to take any corrective actions.
Communication:
To perform the above-mentioned functions, a communication network is required. The following components of a DNC system are linked together via the communication network: machine tool and the host computer, NC part program terminals and the host computer, and connection between a host computer and mass storage.
Advantages of DNC:
DNC systems have advantages over conventional NC systems. Here is a list of some advantages of the DNC system:
• Elimination of perforated tapes: The least reliable component of an NC system, ie the tape reader and perforated tape were eliminated in the event of a
DNC systems. The wired control unit has also been replaced in some cases of DNC systems. These were replaced by specialized control systems.
• Greater flexibility and computational power: Large computers have increased computational power and provided greater data flexibility compared to traditional NC systems. Flexibility resulted from the presence of software rather than wired devices.
• Part program storage: DNC system storage is relatively larger than conventional NC systems that use tapes to store part program instructions. This led to data storage for processing large numbers of machine tools simultaneously.
• Store performance reporting: one of the important functions of the DNC system is to collect data regarding store performance measurement. The processed data can then be analyzed by the managers and hence the store performance monitoring can be kept under control.
DNC FAQ
What is DNC or Direct Numerical Control?
Direct Numerical Control (DNC) is a manufacturing technique that involves the use of a computer network to control and manage multiple machine tools from a central computer. It enables real-time communication between the central computer and individual machine tools, allowing for efficient programming, data storage, and data retrieval.
How does DNC differ from traditional CNC?
While CNC (Computer Numerical Control) relies on local programming and control of individual machine tools, DNC extends the capabilities by incorporating a computer network. DNC allows for centralized control, file management, and data transfer between the central computer and multiple machine tools simultaneously.
What are the advantages of using the DNC?
DNC offers several advantages, including:
Centralized control and monitoring of multiple machine tools.
Reduced programming time and effort by eliminating the need to manually transfer programs to each machine.
Enhanced data management, allowing for efficient storage, retrieval, and version control of programs.
Real-time feedback and diagnostics from machine tools to the central computer.
Improved productivity and efficiency in the manufacturing process.What are the components of a typical DNC system?
A typical DNC system consists of the following components:
Central computer: Acts as the control unit and manages the communication with machine tools.
DNC software: Provides the interface for programming, file management, and data transfer.
Communication network: Enables the connection between the central computer and machine tools.
Machine tools: The individual devices controlled by the DNC system.How does data transfer occur in a DNC system?
Data transfer in a DNC system can be achieved through various methods, such as serial cables, Ethernet, or wireless connections. The central computer sends the program data to the designated machine tool, which receives and executes the instructions.
Can DNC systems handle different types of machine tools?
Yes, DNC systems are designed to be compatible with a wide range of machine tools, including milling machines, lathes, routers, grinders, and more. As long as the machine tool supports DNC connectivity, it can be integrated into the system.
Is DNC suitable for large-scale manufacturing operations?
Yes, DNC is particularly well-suited for large-scale manufacturing operations where multiple machine tools are involved. It allows for centralized control, efficient programming, and seamless coordination between different machines, leading to improved productivity and reduced downtime.
What are the security considerations with DNC systems?
Security is an important aspect of DNC systems, as they rely on network connectivity. Implementing secure network protocols, firewalls, and access controls is crucial to protect against unauthorized access, data breaches, or tampering of program files.
Can DNC systems integrate with other manufacturing technologies?
Yes, DNC systems can integrate with other manufacturing technologies to create a comprehensive production environment. For example, they can be integrated with CAD/CAM software for seamless program generation, or with machine monitoring systems for real-time data collection and analysis.
Are there any alternatives to DNC?
While DNC is a widely used method for controlling machine tools, alternative approaches include using CNC machines with built-in networking capabilities or utilizing cloud-based manufacturing solutions. These alternatives offer similar functionalities but may have different implementation requirements and costs.