Table of Contents
Introduction:
Injection molding is a popular manufacturing process used to produce various plastic products, from car parts to toys. At the heart of this process is the injection molding machine, which uses high pressure and temperature to melt plastic pellets and inject them into a mold to create a desired shape.
What is an injection molding machine?
An injection molding machine is a machine used to produce plastic products through the process of injection molding. This machine is used to melt plastic pellets and inject them into a mold to create a specific shape.
The process is used to produce a wide range of products, including automotive parts, household items, toys, and medical equipment. Injection molding machines come in various sizes and configurations, ranging from small tabletop machines to large industrial machines.
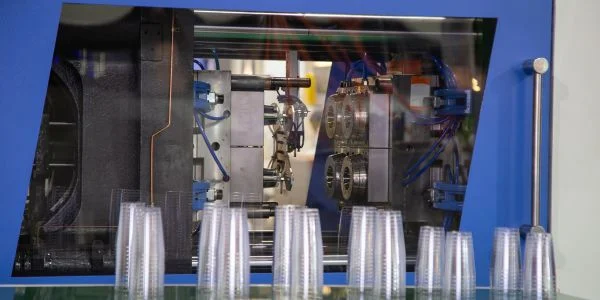
Parts of an injection molding machine
An injection molding machine consists of several parts that work together to create the desired product. These parts include:
1. Hopper:
The hopper is where the plastic pellets are placed before they are fed into the machine. The hopper is usually made of stainless steel and has a capacity of several pounds.
2. Barrel:
The barrel is where the plastic pellets are melted. The barrel is heated to a high temperature using electric heaters or heating bands. The plastic pellets are fed into the barrel through a feed throat.
3. Screw:
The screw is used to move the plastic pellets through the barrel and into the mold. The screw is driven by a motor and has a helical flight that moves the plastic pellets toward the mold.
4. Nozzle:
The nozzle is the part of the machine that connects the barrel to the mold. The melted plastic is forced through the nozzle and into the mold.
5. Mold:
The mold is the part of the machine that creates the desired shape. The mold is made of two halves, and each half is made of steel. The mold is designed to create a specific shape, and the plastic is injected into the mold under high pressure.
6. Clamping unit:
The clamping unit is used to hold the mold together during the injection process. The clamping unit is made up of several parts, including the clamping plate, the platen, and the tie bars. The clamping unit is designed to hold the mold together with enough force to withstand the high pressure of the injection process.
How does an injection molding machine work?
The injection molding process begins with the plastic pellets being fed into the hopper. From there, the plastic pellets are moved into the barrel using a screw. The barrel is heated to a high temperature, and the plastic pellets are melted.
Once the plastic is melted, the screw moves the melted plastic toward the mold. The plastic is forced through the nozzle and into the mold, where it is cooled and solidified.
The clamping unit holds the mold together during the injection process, and the high pressure of the injection process ensures that the plastic fills the mold completely.
Once the plastic has cooled and solidified, the mold is opened, and the finished product is removed from the mold. The process then repeats, with the plastic pellets being fed into the hopper to create another product.
Types of injection molding machines:
There are several types of injection molding machines available, each with its own unique advantages and disadvantages. Some of the most common types include:
1. Hydraulic Injection Molding Machines:
These machines use hydraulic power to generate pressure and control the movement of the mold. They are known for their high production rates and are typically used for large-scale production runs.
Advantages:
– High production rates
– Low maintenance costs
– Capable of producing large parts
Disadvantages:
– High initial investment costs
– Slow cycle times
– Requires large floor space
2. Electric Injection Molding Machines:
These machines use electric motors to drive the hydraulic system, which helps to improve energy efficiency and reduce operating costs. They are known for their precision and accuracy and are commonly used for small to medium-sized production runs.
Advantages:
– High precision and accuracy
– Energy efficient
– Faster cycle times
Disadvantages:
– High initial investment costs
– Limited production capacity
– Requires skilled operators
3. Hybrid Injection Molding Machines:
These machines combine the best features of hydraulic and electric machines. They use both hydraulic and electric systems to provide high production rates, energy efficiency, and precision.
Advantages:
– High production rates
– Energy efficient
– High precision and accuracy
Disadvantages:
– High initial investment costs
– Requires skilled operators
– Limited production capacity
Applications of Injection Molding Machines:
Injection molding machines are used to produce a wide range of plastic products, from small components to large automotive parts. Some common applications include:
1. Consumer Goods:
Injection molding machines are used to produce a variety of consumer goods, including toys, household appliances, and electronic components.
2. Medical Devices:
Injection molding machines are used to produce medical devices such as syringes, IV tubing, and surgical instruments.
3. Automotive Industry:
Injection molding machines are used to produce various automotive parts such as dashboards, bumpers, and interior trim.
4. Packaging Industry:
Injection molding machines are used to produce a variety of packaging materials such as bottles, caps, and closures.
Also, read waterjet machine
Comment on “Injection molding machine – Types, Working, Advantages”
Comments are closed.