Table of Contents
Definition of a Cornish Boiler
A Cornish boiler is a type of horizontal, fire-tube boiler widely used during the 19th century. It was named after its place of origin, Cornwall, England, where it was developed by engineer Richard Trevithick in 1812. Cornish boilers are known for their simplicity and reliability, making them popular in industries such as mining, textile manufacturing, and power generation.
Parts of a Cornish Boiler
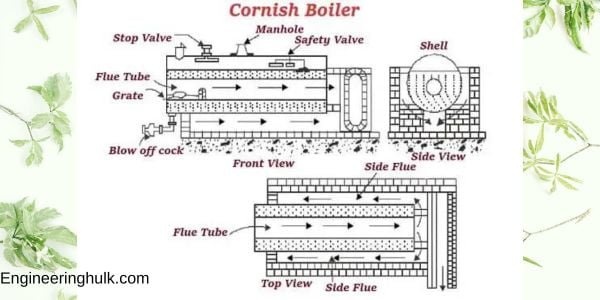
1. Shell:
The shell is the main body of the Cornish boiler, typically cylindrical in shape and constructed from wrought iron or steel plates. It houses the various components of the boiler and contains the water and steam.
2. Furnace Tube:
The furnace tube, also known as the combustion chamber, is located at the front end of the boiler. It is where the fuel, such as coal or wood, is burned to generate heat. The hot gases produced during combustion travel through the furnace tube before reaching the other parts of the boiler.
3. Grate:
The grate is a metal structure positioned inside the furnace tube. Its purpose is to support the fuel and allow air to pass through for efficient combustion. The grate can be manually or mechanically operated to control the flow of fuel.
4. Combustion Chamber:
The combustion chamber is the area where the fuel is burned, and heat is generated. It is connected to the furnace tube and allows the hot gases to pass through, transferring their heat energy to the surrounding water.
5. Flue Tubes:
Cornish boilers have a single flue tube that runs through the entire length of the boiler shell. It connects the combustion chamber to the smokebox, allowing the hot gases to pass through and release the remaining heat before exiting through the chimney.
6. Water Space:
The water space refers to the region within the shell where the water is stored. It surrounds the flue tube, maximizing the heat transfer from the combustion gases to the water.
7. Steam Space:
The steam space is located above the water level within the boiler shell. It serves as a reservoir for steam generated from the heated water. The steam is collected here before being supplied to the machinery or process that requires it.
8. Manhole:
The manhole is an opening in the boiler shell designed for maintenance and inspection purposes. It provides access to the interior of the boiler, allowing technicians to inspect, clean, and repair the various components.
9. Safety Valves:
Safety valves are crucial components of any boiler, including Cornish boilers. They are responsible for releasing excess pressure to prevent catastrophic failures. In Cornish boilers, safety valves are usually mounted on the boiler shell to discharge steam when the pressure exceeds a predetermined limit.
Working of a Cornish Boiler
Cornish boilers operate on the principle of generating steam through the combustion of fuel. Here’s a step-by-step breakdown of their working mechanism:
1. Combustion:
The fuel, typically coal or wood, is ignited in the furnace tube, which is located at the front end of the boiler. The burning fuel releases heat energy, creating a high-temperature environment.
2. Heat Transfer:
The hot gases produced during combustion travel through the furnace tube, transferring their heat energy to the water surrounding the flue tube. The water absorbs this heat and starts to rise in temperature.
3. Steam Generation:
As the water absorbs more heat, it eventually reaches its boiling point and undergoes a phase change, converting it into steam. The steam separates from the water and rises to the steam space located above the water level within the boiler shell.
4. Steam Collection:
The steam collected in the steam space is then channeled out through the steam outlet to supply power to machinery or industrial processes that require steam.
Advantages of Cornish Boilers
1. Simple Design:
Cornish boilers boast a straightforward design, making them easy to manufacture, operate, and maintain. This simplicity also contributes to their reliability.
2. Efficiency:
Cornish boilers have a high thermal efficiency due to their large heating surface area and effective heat transfer mechanism. This efficiency leads to optimal fuel consumption and reduced operating costs.
3. Compact Size:
Compared to other types of boilers, Cornish boilers have a relatively compact size, making them suitable for installation in limited spaces.
4. Safety:
Cornish boilers incorporate safety valves that prevent excessive pressure buildup, ensuring safe operation and protecting against potential accidents.
Disadvantages of Cornish Boilers
1. Slow Steam Generation:
Cornish boilers have a slower steam generation rate compared to some other boiler types. This limitation may impact their suitability for high-demand applications.
2. Limited Pressure Range:
Cornish boilers are best suited for low to moderate-pressure applications. They may not be suitable for industries requiring high-pressure steam.
3. Heat Loss:
Cornish boilers may experience heat losses through the boiler shell due to their exposed flue tubes, leading to lower overall efficiency.
Applications of Cornish Boilers
1. Textile Industry:
Cornish boilers were widely used in textile manufacturing during the industrial revolution to power machinery such as spinning frames and weaving looms.
2. Mining Industry:
Cornish boilers played a crucial role in the mining industry, providing steam power for hoists, pumps, and other mining equipment.
3. Breweries and Distilleries:
Cornish boilers were employed in breweries and distilleries to facilitate the brewing and distillation processes.
4. Power Generation: Cornish boilers were utilized in small-scale power generation for electricity or mechanical power in industries.
Also, read the Loeffler boiler
Comment on “Cornish Boiler – Parts, working, Advantages, Applications”
Comments are closed.