Table of Contents
Introduction:
The theories of failure are essential concepts in engineering that explain the behavior of materials under different loading conditions. Understanding these theories is crucial for designing safe and reliable structures.
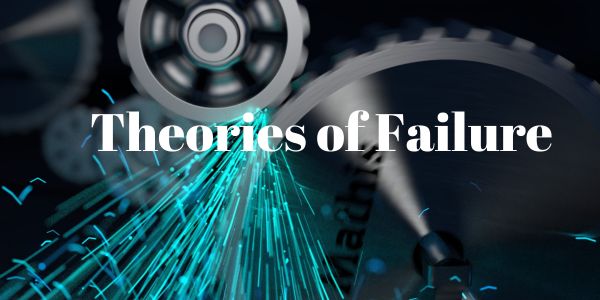
Theories of Failure Types:
Theories of failure are based on the loading condition (tensile load, compressive load, and shear load) and material behavior (ductile, plastic, and brittle) are:
Tensile Load:
The tensile load is a type of loading condition in which a material experiences a stretching force. The theories of failure associated with tensile load are as follows:
1. Maximum normal stress theory: This theory states that failure occurs when the maximum normal stress in a material exceeds its ultimate tensile strength (UTS). The UTS is the maximum stress a material can withstand before it fails. This theory is applicable to brittle materials such as ceramics and glass.
2. Maximum shear stress theory: This theory states that failure occurs when the maximum shear stress in a material exceeds its shear strength. The shear strength is the maximum stress a material can withstand before it fails in shear. This theory is applicable to ductile materials such as metals.
3. Strain energy theory: This theory states that failure occurs when the strain energy per unit volume in a material exceeds its strain energy capacity. The strain energy capacity is the maximum amount of energy a material can absorb before it fails. This theory is applicable to both brittle and ductile materials.
Compressive Load:
The compressive load is a type of loading condition in which a material experiences a compressing force. The theories of failure associated with compressive load are as follows:
1. Maximum normal stress theory: This theory states that failure occurs when the maximum normal stress in a material exceeds its compressive strength. Compressive strength is the maximum stress a material can withstand before it fails in compression. This theory is applicable to brittle materials such as concrete and masonry.
2. Maximum shear stress theory: This theory states that failure occurs when the maximum shear stress in a material exceeds its shear strength. This theory is applicable to ductile materials such as metals.
3. Strain energy theory: This theory is also applicable to both brittle and ductile materials under compressive loading.
Shear Load:
The shear load is a type of loading condition in which a material experiences a shearing force. The theories of failure associated with shear load are as follows:
1. Maximum distortion energy theory: This theory states that failure occurs when the distortion energy per unit volume in a material exceeds its distortion energy capacity. The distortion energy capacity is the maximum amount of energy a material can absorb before it fails in shear. This theory is applicable to ductile materials such as metals.
2. Maximum shear stress theory: This theory is also applicable to shear loading.
Material Behavior:
Material behavior refers to the response of a material to an external load. The theories of failure associated with material behavior are as follows:
1. Ductile materials: Ductile materials are those that undergo significant plastic deformation before they fail. Theories such as maximum shear stress theory and strain energy theory are applicable to ductile materials.
2. Plastic materials: Plastic materials are those that undergo significant plastic deformation before they fail, but their failure is not accompanied by a large amount of energy absorption. Theories such as maximum normal stress theory and maximum shear stress theory are applicable to plastic materials.
3. Brittle materials: Brittle materials are those that fail suddenly without significant plastic deformation. Theories such as maximum normal stress theory and maximum shear stress theory are applicable to brittle materials.
Theories of Failure:
The analysis of structural components under load is critical in ensuring that they are able to safely withstand the applied stresses. Failure theories are used to determine the failure modes and design criteria for various structural materials. There are several theories of failure, including maximum principal strain theory, maximum shear stress theory, and maximum strain energy theory.
Maximum Principal Strain Theory
The maximum principal strain theory states that failure occurs when the maximum principal strain in a material exceeds a critical value. The maximum principal strain is the largest of the three principal strains and is calculated using the following formula:
ε1 = (σ1 – σ2) / E
where σ1 and σ2 are the maximum and minimum normal stresses, respectively, and E is the modulus of elasticity.
The critical value of maximum principal strain depends on the material properties and is obtained experimentally. This theory is applicable to brittle materials such as ceramics, where failure is predominantly due to tensile stresses.
Maximum Shear Stress Theory
The maximum shear stress theory states that failure occurs when the maximum shear stress in a material exceeds a critical value. The maximum shear stress is calculated using the following formula:
τmax = (σ1 – σ2) / 2
where σ1 and σ2 are the maximum and minimum normal stresses, respectively.
The critical value of maximum shear stress depends on the material properties and is obtained experimentally. This theory is applicable to ductile materials such as metals, where failure is predominantly due to shear stresses.
Maximum Strain Energy Theory
The maximum strain energy theory states that failure occurs when the maximum strain energy in a material exceeds a critical value. The maximum strain energy is calculated using the following formula:
U = (1/2) [ ((σ1 – σ2)^2 + (σ2 – σ3)^2 + (σ1 – σ3)^2) / E ]
where σ1, σ2, and σ3 are the principal stresses and E is the modulus of elasticity.
The critical value of maximum strain energy depends on the material properties and is obtained experimentally. This theory is applicable to ductile materials such as metals, where failure is predominantly due to the deformation of the material.
Design Conditions for Various Failure Theories with Derivation
The design conditions for each of the failure theories are based on the stress state at a point in the material. The three principal stresses, σ1, σ2, and σ3, are determined from the stress components using the following equations:
σ1 = (σx + σy) / 2 + sqrt((σx – σy)^2 / 4 + τxy^2)
σ2 = (σx + σy) / 2 – sqrt((σx – σy)^2 / 4 + τxy^2)
σ3 = σz
where σx, σy, and σz are the normal stresses in the x, y, and z directions, respectively, and τxy is the shear stress in the xy plane.
For the maximum principal strain theory, the design condition is:
ε1 < ε1c
where ε1c is the critical value of maximum principal strain.
For the maximum shear stress theory, the design condition is:
τmax < τmaxc
where τmaxc is the critical value of maximum shear stress.
For the maximum strain energy theory, the design condition is:
U < Uc
where Uc is the critical value of maximum strain energy.
The selection of a failure theory depends on the material properties and the type of stress state being analyzed. The critical values for each theory must be determined by experiment.
Also, read the mechanical properties of materials
Comment on “Theories of Failure – Detailed Explanation with Derivation”
Comments are closed.