Table of Contents
In engineering and manufacturing, the concept of tolerances is paramount to ensuring components fit and function properly. At its core, tolerance refers to the permissible limit or limits of variation in a physical dimension.
Introduction to Tolerances
Tolerances are foundational in the manufacturing and assembly process of nearly every product or system. They are predefined allowable variations that ensure parts can consistently be manufactured and assembled with precision, yet without imposing unrealistic or unattainable standards.
To put it simply, if a bolt is designed to fit a hole, the hole cannot be precisely the same size as the bolt. If it were, even the slightest oversize of the bolt or undersize of the hole would result in a misfit. Hence, both the bolt and hole would have a certain allowable size variation, which ensures they fit under various conditions.
Importance of Tolerances
- Consistency and Interchangeability: Tolerances ensure that parts manufactured in large numbers will consistently fit together. This means a part produced in one batch, or even at a different location, will work seamlessly with others due to these standard variations.
- Safety: In critical applications, especially in industries like aerospace or medical devices, tight tolerances are necessary to guarantee safety. Inappropriate tolerances can lead to failures that could jeopardize lives.
- Cost-efficiency: Specifying unnecessarily tight tolerances can be expensive. It’s vital to balance the precision required for functionality with economical production techniques.
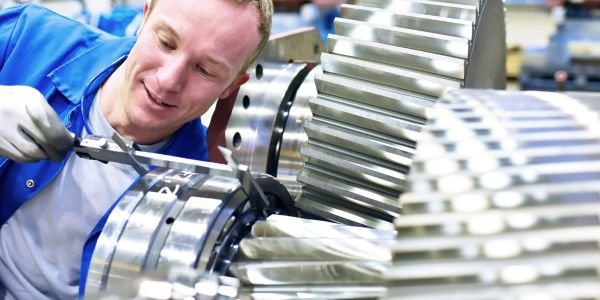
Types of Tolerances
Unilateral Tolerance
Unilateral tolerances are when variations are permitted in only one direction from the nominal dimension. For example, if a 10mm rod can only be 10.1mm and no less, then it has a unilateral tolerance of +0.1mm.
Bilateral Tolerance
This type allows variation in both directions from the nominal dimension. Using the same example, if the rod can be between 9.9mm and 10.1mm, it has a bilateral tolerance of ±0.1mm.
Limit Tolerance
This indicates the upper and lower permissible sizes for a dimension. For the rod, the upper limit might be 10.1mm, and the lower limit might be 9.9mm.
Methods to Specify Tolerance
Limit Dimensions
Here, the maximum and minimum sizes are directly given. For example, 9.9mm to 10.1mm.
Plus-Minus Dimensions
A base dimension with permissible variations, like 10mm ±0.1.
Geometric Tolerance
This is specified for attributes like flatness, straightness, and concentricity, often using symbols on technical drawings.
Basic table showing some common factors that influence tolerance selection, along with general information about each factor:
Factor | Description | General Tolerance Considerations |
Material | The material from which a part is made. | – Different materials may shrink or expand differently during manufacturing – Some materials may be harder to machine or mold with precision. |
Manufacturing Process | How the part is made (e.g., milling, casting, molding). | – Precision machining can achieve tighter tolerances than casting – Molding processes might have variances due to cooling rates. |
Size | Overall size of the component. | – Larger parts might have more significant variances due to material behavior and processing challenges. |
Application | The intended use of the part (e.g., aerospace, automotive). | – Critical applications like aerospace often demand tighter tolerances – Consumer applications might have more lenient requirements. |
Fit Requirement | How the part needs to fit with other parts (e.g., loose fit, press fit). | – Tighter fits generally require tighter tolerances – Some fits might allow for more slack or play. |
Temperature | Operating temperature range of the part. | – Parts operating in varying temperatures may need to account for expansion or contraction. |
Load & Stress | Mechanical stresses the part will be subjected to. | – High-stress parts might require more stringent tolerances to ensure safety and functionality. |
Finish & Appearance | Cosmetic requirements of the part. | – Surface finish might affect fit or function. <br> – Cosmetic parts might have tighter tolerances on visible surfaces. |
This table provides a general overview, and real-world applications will often need to dive into specific standards and conduct analysis to determine the exact tolerances required. Engineers should always consult relevant standards, conduct necessary tests, and work closely with manufacturers when specifying tolerances.
Factors Influencing Tolerance Choices
- Material properties: Materials can expand or contract under various conditions. Metals, for instance, might expand with temperature, requiring different tolerances based on operating conditions.
- Manufacturing process: Processes like casting may have more variability than precision machining, leading to different tolerances.
- Intended use: A precision instrument in a laboratory will likely have tighter tolerances than a workshop hammer.
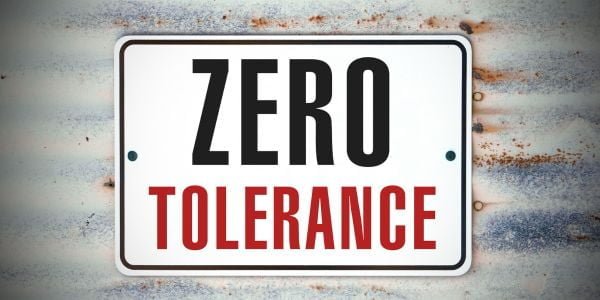
Tolerance Stacking
When multiple components with tolerances are assembled, the cumulative effect — often termed “tolerance stacking” or “tolerance buildup” — can become a challenge. Engineers must ensure that even in the worst-case scenario of all components being at their maximum or minimum tolerances, the final assembly still functions correctly.
Implications of Incorrect Tolerances
- Functional Failure: Parts might not fit, or assemblies may not function if tolerances are inappropriate.
- Increased Costs: Overly tight tolerances can lead to increased inspection and rejection rates, raising manufacturing costs.
- Reduced Production Speed: Achieving very tight tolerances might require slower, more deliberate processes, impacting production rates.
Standards and Guidelines
Various international organizations, such as the International Organization for Standardization (ISO) and the American Society of Mechanical Engineers (ASME), provide guidelines and standards for engineering tolerances to ensure consistency and interoperability across industries and nations.
Tolerances are an integral aspect of engineering, bridging the gap between design and manufacturing. A deep understanding of tolerances ensures that components are manufactured efficiently, safely, and effectively, fulfilling their intended function in the broader assembly or system.
In today’s globalized world, with components sourced from around the globe, adhering to internationally recognized tolerance standards is ever more crucial. Thus, every engineer, irrespective of their specialization, must be well-versed in the intricacies of general engineering tolerances.
Also, read EDM Machine
Comment on “General Engineering Tolerances: Types, Methods & More”
Comments are closed.