Table of Contents
Brazing is a versatile and widely used metal joining process that has been employed for centuries to create strong and durable bonds between metals. Whether you’re a professional metalworker or just curious about the world of metallurgy.
What is Brazing?
Brazing is a metal-joining process that relies on the principle of capillary action to fuse two or more metal pieces. Unlike welding, which melts the base metals, brazing uses a filler metal with a lower melting point than the workpieces being joined. This filler metal is drawn into the gap between the pieces to be joined, creating a strong and durable bond when it solidifies.
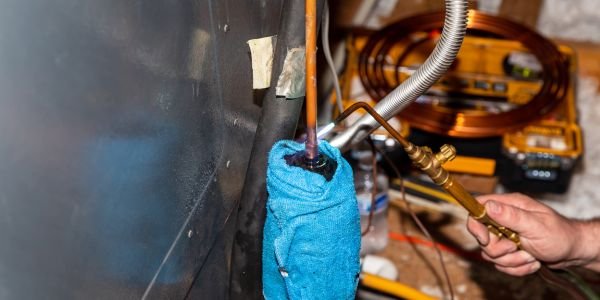
The Brazing Process
Brazing involves several key steps:
Surface Preparation:
Before brazing, it’s crucial to prepare the metal surfaces. This typically involves cleaning the workpieces to remove any contaminants like grease, rust, or oxides. Clean surfaces ensure better adhesion and a stronger bond.
Assembly:
The pieces to be joined are carefully aligned and assembled, ensuring they fit together with the desired gap. Fixtures or clamps may be used to hold them in place during brazing.
Flux Application:
Flux is a critical component of the brazing process. It serves several purposes: it removes oxides from the metal surfaces, prevents further oxidation during heating, and promotes the flow of the filler metal. Flux is applied to the joint area either as a paste or in a liquid form.
Heating:
The assembly is heated using a torch, furnace, or other heating methods. The filler metal is introduced near the joint, and as it melts, capillary action draws it into the gap between the workpieces. The filler metal should be heated above its melting point but below the melting point of the base metals.
Solidification:
Once the filler metal flows into the joint and fills the gap, it solidifies, creating a strong bond between the workpieces. The assembly is then allowed to cool slowly to prevent thermal stress.
Brazing Filler Metals
The choice of filler metal is crucial in brazing as it determines the characteristics of the joint, such as its strength and temperature resistance. Common brazing filler metals include:
- Silver-based Alloys: Known for their high strength and excellent electrical conductivity, silver-based filler metals are commonly used in electrical and electronic applications.
- Copper-based Alloys: These fillers are versatile and well-suited for joining copper, brass, and bronze.
- Nickel-based Alloys: Nickel fillers are ideal for applications that require resistance to corrosion and high temperatures.
- Aluminum-based Alloys: Aluminum fillers are used for joining aluminum and its alloys, offering good corrosion resistance.
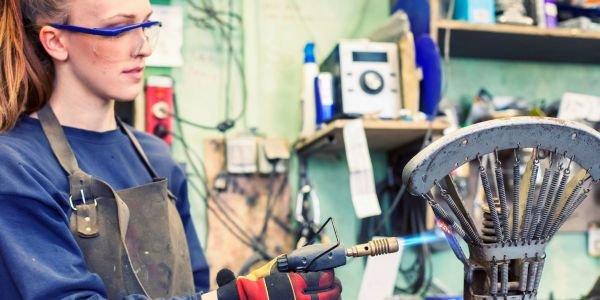
Applications of Brazing
Brazing finds applications in various industries due to its versatility and strength:
- Automotive: Brazing is used in the fabrication of exhaust systems, radiators, and air conditioning components.
- Aerospace: Aircraft engines, heat exchangers, and structural components often rely on brazed joints for their strength and reliability.
- Plumbing: Brazing is commonly used to join copper pipes and fittings in plumbing systems.
- Electronics: The high electrical conductivity of silver-based brazing alloys makes them ideal for joining electrical components.
- Jewelry: Fine jewelry often involves intricate brazing work to join precious metals.
Advantages of Brazing
Brazing offers several advantages over other metal-joining processes, including:
- Lower Heat Input: Brazing uses lower temperatures than welding, reducing the risk of warping or distortion in the workpiece.
- Versatility: It can join dissimilar metals, making it suitable for a wide range of applications.
- Clean Joints: Brazing produces clean, aesthetically pleasing joints with minimal splatter and spatter.
- High Joint Strength: Brazed joints are often stronger than the base metals being joined.
Disadvantages of Brazing
While brazing offers numerous advantages, it also has its limitations and disadvantages that should be considered in various applications:
- Limited Joint Strength: While brazed joints are generally strong, they may not be as strong as those produced by welding or other joining methods. This limitation can be a concern in applications where extremely high joint strength is required.
- Temperature Sensitivity: Brazing requires precise temperature control. If the base metals are heated too much, they can lose their properties, deform, or even melt. Conversely, if the temperature is too low, the filler metal may not flow properly, leading to weak or incomplete joints.
- Joint Appearance: Although brazing produces clean and aesthetically pleasing joints, the appearance of the joint can be a disadvantage in some applications where a seamless or nearly invisible joint is desired.
- Limited Applicability to Non-Metals: Brazing is primarily used for joining metals and is not suitable for joining non-metallic materials, such as ceramics or plastics.
- Cost of Filler Materials: High-quality filler metals, such as silver-based alloys, can be expensive. The cost of filler materials can be a significant consideration in large-scale or cost-sensitive applications.
- Complexity: Brazing requires careful preparation, including surface cleaning, flux application, and precise temperature control. This complexity can make the process more time-consuming and may require skilled operators.
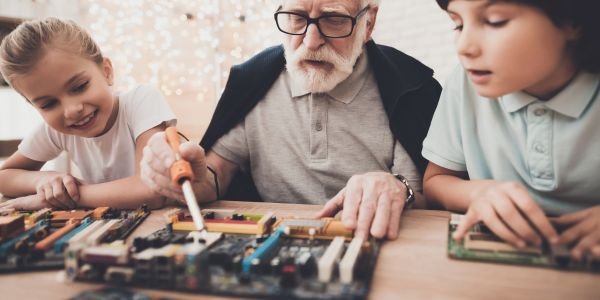
Applications of Brazing
Brazing is a versatile joining process with a wide range of applications across various industries. Some of the key applications include:
- Aerospace: Brazing is used extensively in the aerospace industry to join components like heat exchangers, turbine blades, and structural elements. It offers the necessary strength and reliability for critical aircraft systems.
- Automotive: Brazing is employed in the manufacture of automotive components, including exhaust systems, radiators, and air conditioning parts. It ensures leak-free and durable joints in these systems.
- Electronics: The electrical conductivity of silver-based brazing alloys makes them ideal for joining electrical and electronic components, such as connectors, switches, and circuit boards.
- Plumbing and HVAC: Copper pipes and fittings are often joined using brazing in plumbing and heating, ventilation, and air conditioning (HVAC) systems. Brazed joints are resistant to leaks and corrosion.
- Jewelry Making: Fine jewelry often involves brazing to join precious metals like gold and silver. Brazing allows for intricate and precise metalwork in jewelry design.
- Power Generation: Brazing is used in the production of heat exchangers and other components in power generation systems, such as boilers and condensers.
- Medical Devices: Brazing is employed in the medical industry to create strong and biocompatible joints for devices like surgical instruments and dental tools.
- Instrumentation: Brazing is used to assemble precise instruments and sensors, ensuring a secure and hermetic seal between components.
- Food Processing Equipment: In the food industry, brazing is utilized to fabricate equipment like heat exchangers and stainless steel components that require corrosion resistance and hygiene.
- Art and Sculpture: Artists and sculptors use brazing to create metal sculptures and art pieces due to their ability to join various metals and provide clean, aesthetically pleasing joints.
Brazing is a time-tested and versatile metal-joining process with applications spanning numerous industries. Its ability to create strong, clean, and reliable joints makes it a valuable technique for joining a wide range of materials. Whether you’re working on automotive components, aerospace structures, or intricate jewelry, brazing is a skill worth mastering for any metallurgist or metalworker.
Understanding the process and selecting the appropriate filler metal is key to achieving successful brazed joints that meet the specific requirements of your project.