Table of Contents
What is a Waterjet Machine?
A waterjet machine is a piece of equipment that uses a high-pressure stream of water to cut through various materials. This technology is used in a variety of industries, including aerospace, automotive, and manufacturing. Waterjet machines are capable of cutting through materials such as metal, wood, plastics, stone, and ceramics.
Waterjet machines work by accelerating water to high speeds and then directing it through a small nozzle. The nozzle is typically made from diamond or sapphire, which is able to withstand the high pressures and abrasion caused by the water. The water is forced through the nozzle using a high-pressure pump, which can produce pressures of up to 90,000 psi (pounds per square inch).
The high-pressure stream of water is capable of cutting through materials due to its velocity and kinetic energy. When the water is forced through the nozzle, it creates a small stream of water that travels at speeds of up to Mach 3 (2,300 mph). The water stream is so powerful that it can cut through materials with ease, without the need for additional heat or chemicals.
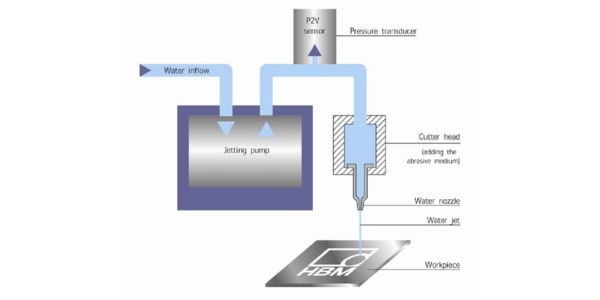
Parts of a Waterjet Machine
A waterjet machine is comprised of several key components, each of which plays an important role in the cutting process. The main components of a waterjet machine include:
1. High-Pressure Pump:
The high-pressure pump is responsible for generating the pressure required to propel the water through the nozzle. The pump is typically powered by an electric motor or a diesel engine and is capable of producing pressures of up to 90,000 psi.
2. Water Reservoir:
The water reservoir is used to store and supply water to the pump. The reservoir is typically made from stainless steel or plastic and is designed to withstand the high pressures produced by the pump.
3. High-Pressure Hose:
The high-pressure hose is used to transport the water from the pump to the cutting head. The hose is typically made from reinforced rubber or thermoplastic and is designed to withstand the high pressures and abrasion caused by the water.
4. Cutting Head:
The cutting head is part of the machine that directs the water stream toward the material being cut. The cutting head typically includes a nozzle, which is used to focus the water into a narrow stream. The cutting head may also include a mixing chamber, which is used to mix abrasive materials with water to increase cutting power.
5. Abrasive Delivery System (optional):
An abrasive delivery system is an optional component that can be added to a waterjet machine to increase cutting power. The abrasive delivery system uses a separate hopper to introduce abrasive materials into the water stream, which helps to cut through harder materials.
How Does a Waterjet Machine Work?
A waterjet machine operates by following these basic steps:
Step 1: Pressurizing Water
The first step in the process is to pressurize the water. Water is drawn from a reservoir and then pumped through a high-pressure pump. The pressure can be as high as 90,000 PSI, depending on the type of material being cut.
Step 2: Mixing Abrasive Particles
Next, abrasive particles are mixed with the pressurized water. The abrasive particles are typically made from garnet, which is a hard and dense mineral that is capable of cutting through a wide range of materials.
Step 3: Directing the Jet
The high-pressure water mixed with abrasive particles is then directed through a nozzle. The nozzle is typically made from tungsten carbide, which is capable of withstanding the high-pressure and abrasive nature of the water jet. The nozzle size and shape can be adjusted to control the flow of the water jet and the size of the cutting stream.
Step 4: Cutting the Material
Once the water jet is directed toward the material, it begins to cut through it. The high-pressure water stream mixed with abrasive particles erodes the material, creating a clean and precise cut. The cutting speed depends on the type of material being cut, but waterjet machines are generally fast and efficient.
Benefits of Waterjet Machines
Waterjet machines have many benefits compared to other cutting methods, including:
1. Precision: Waterjet machines are capable of cutting with high precision, producing a clean and accurate cut without any heat-affected zone.
2. Versatility: Waterjet machines can cut through a wide range of materials, including metals, plastics, glass, stone, and composites.
3. No heat-affected zone: Unlike traditional cutting methods that use heat to cut, waterjet machines do not produce a heat-affected zone, reducing the risk of warping or damaging the material.
4. Environmentally friendly: Waterjet machines do not produce hazardous waste, making them an environmentally friendly choice.
5. Reduced material waste: Waterjet machines are capable of cutting very close to the material edge, reducing material waste and saving money.
Types of waterjet machines available in the market
1. Pure waterjet machines:
As the name suggests, pure waterjet machines use only high-pressure water to cut materials. These machines are ideal for cutting soft materials such as foam, rubber, and textiles. Pure waterjet machines are also used for cutting materials that are sensitive to heat or prone to melting.
2. Abrasive waterjet machines:
Abrasive waterjet machines, on the other hand, use a mixture of water and abrasive particles to cut harder materials such as metals, ceramics, and composites. The abrasive particles are usually made of garnet, which is a type of hard rock. The mixture of water and abrasive particles is forced through a small nozzle at high speed, creating a powerful cutting stream.
3. Hybrid waterjet machines:
Hybrid waterjet machines combine the capabilities of both pure waterjet and abrasive waterjet machines. These machines can switch between pure waterjet and abrasive waterjet modes, depending on the material being cut. Hybrid waterjet machines are versatile and can cut a wide range of materials, from soft foams to hard metals.
4. Portable waterjet machines:
Portable waterjet machines are smaller, lighter, and more compact than traditional waterjet machines. These machines are designed to be easily transported and set up on-site, making them ideal for mobile cutting applications. Portable waterjet machines are commonly used in industries such as construction, demolition, and mining.
5. Robotic waterjet machines:
Robotic waterjet machines use robotic arms to control the cutting process. These machines are ideal for cutting complex shapes and patterns in materials that require high precision, such as automotive parts or aerospace components. Robotic waterjet machines can also be used for 3D cutting applications, such as cutting curved or angled surfaces.
Also, read Laser cutting machine
Comment on “Waterjet machine – Types, Working & Benefits”
Comments are closed.