Table of Contents
Introduction
Benson boilers are high-pressure, drumless, water tube boilers widely used in power plants and other industrial applications. Developed by Mark Benson in the 1920s, these boilers revolutionized the power generation industry due to their exceptional efficiency and safety features.
Definition of Benson Boilers
A Benson boiler is a type of supercritical, once-through boiler that operates at high pressure and temperature. Unlike conventional drum-type boilers, Benson boilers do not rely on steam drums for steam-water separation. Instead, they employ a unique design that allows water to flow through the boiler tubes in a single pass, transforming it into supercritical steam.
Parts of Benson Boilers
1. Economizer
The economizer is the first component encountered in the Benson boiler. It preheats the incoming feedwater using the heat of the flue gases, increasing overall efficiency. By utilizing this waste heat, the economizer significantly reduces fuel consumption and exhaust emissions.
2. Evaporator Tubes
Evaporator tubes are an essential part of the Benson boiler, responsible for heat transfer and the conversion of water into supercritical steam. These tubes are designed to withstand high temperatures and pressures. The supercritical steam produced in the evaporator tubes is used to drive the steam turbine and generate electricity.
3. Downcomers
Downcomers are vertical pipes that transport water from the steam drum to the evaporator tubes. They facilitate the natural circulation of water through the boiler system and help maintain stable water levels in the drum.
4. Water Walls
Water walls, also known as boiler tubes or furnace walls, surround the combustion chamber. They absorb the radiant heat generated by the burning fuel and transfer it to the water circulating within the tubes. Water walls also contribute to the structural integrity of the boiler.
5. Superheaters
Superheaters are heat exchangers located in the path of flue gases after the water walls. They further increase the temperature of the steam beyond its saturation point, improving its thermal energy and ensuring maximum efficiency in power generation.
6. Reheaters
Reheaters are additional heat exchangers placed between the low-pressure and high-pressure stages of the steam turbine. They reheat the steam to a specific temperature after it expands in the high-pressure stage, enhancing its thermodynamic properties and overall performance.
7. Separator
The separator is a crucial component in Benson boilers, responsible for separating the water droplets from the steam before it enters the turbine. This separation process prevents damage to the turbine blades, ensuring reliable and efficient power generation.
8. Steam Drum
Although Benson boilers are drumless, they still feature a small steam drum. The steam drum acts as a surge tank, accommodating fluctuations in steam flow and helping to maintain a steady supply of steam to the turbine.
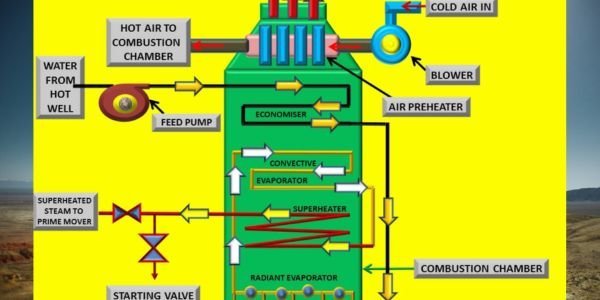
Working Principle of Benson Boilers
The working principle of Benson boilers is based on the principle of forced circulation and once-through operation. Unlike conventional boilers that rely on steam drums for steam-water separation, Benson boilers operate at supercritical pressure, where water and steam exist in a single phase.
The working steps of a Benson boiler are as follows:
1. High-Pressure Feedwater Heating:
The feedwater enters the economizer, where it is preheated using the waste heat from the flue gases.
2. Evaporation:
The preheated water enters the evaporator tubes, which are designed to withstand high temperatures and pressures. As the water flows through the tubes, it absorbs heat from the combustion gases, reaching its critical temperature and pressure, and transforming into supercritical steam.
3. Superheating:
The supercritical steam passes through superheaters, which further increases its temperature beyond its saturation point. This ensures maximum thermal energy and efficiency.
4. Separation:
Before entering the steam turbine, the supercritical steam is passed through a separator, where any remaining water droplets are separated from the steam. This separation process prevents damage to the turbine blades.
5. Power Generation:
The supercritical steam, now dry and high in energy, enters the steam turbine, where it drives the turbine blades, generating electricity. The steam is then condensed and recycled back to the boiler for reuse.
Advantages of Benson Boilers
1. Increased Efficiency:
Benson boilers operate at supercritical pressure, which allows for higher efficiency compared to subcritical boilers. The absence of steam drums and the once-through operation eliminate the need for reheating, resulting in improved overall efficiency.
2. Rapid Start-up:
Benson boilers have the advantage of rapid start-up due to the absence of steam drums. They can quickly reach their operating conditions, reducing the warm-up time and increasing operational flexibility.
3. Compact Design:
The drumless design of Benson boilers makes them more compact and lighter compared to traditional drum-type boilers. This enables easier installation and reduces space requirements.
4. Enhanced Safety:
The supercritical operation of Benson boilers enhances safety by eliminating the risk of explosions caused by steam drum failure. The once-through design also ensures better control over water chemistry, minimizing the potential for corrosion and scaling.
Disadvantages of Benson Boilers
1. Complexity:
Benson boilers are more complex in design and operation compared to conventional boilers. This complexity requires careful engineering, precise control, and specialized maintenance expertise.
2. Cost:
The advanced design and construction of Benson boilers can result in higher initial costs compared to traditional boilers. However, their long-term operational efficiency and savings can offset the initial investment.
Applications of Benson Boilers
Benson boilers find applications in various industries, including:
1. Power Generation:
Benson boilers are widely used in power plants, especially in large-scale, high-capacity power generation facilities. Their high efficiency, quick start-up, and improved safety make them suitable for meeting the increasing electricity demands.
2. Industrial Processes:
Benson boilers are employed in industries such as petrochemicals, refineries, chemical plants, and pulp and paper mills. They provide reliable steam generation for process heating, power, and cogeneration applications.
3. Combined Heat and Power (CHP) Systems:
Benson boilers are utilized in combined heat and power systems, where they generate steam for both electricity production and district heating purposes. This integrated approach maximizes energy utilization and reduces overall carbon emissions.
Also, read Lamont boiler
Comment on “Benson Boilers: Definition, Parts, Advantages, Disadvantages”
Comments are closed.