Table of Contents
Introduction
In the world of modern manufacturing and rapid prototyping, few technologies have captured the imagination quite like 3D printing. Also known as additive manufacturing, this groundbreaking technology has revolutionized various industries, enabling the creation of intricate and customized objects with unparalleled precision.
What is 3D Printing?
At its core, 3D printing is an additive manufacturing process that constructs three-dimensional objects by layering materials on top of each other. Unlike traditional subtractive manufacturing, where the material is removed from a solid block, 3D printing builds objects layer by layer, based on a digital model. This digital model, often created using computer-aided design (CAD) software, serves as the blueprint for the physical object to be printed.
How Does 3D Printing Work?
The process of 3D printing involves several key steps:
1. Designing the Model:
The first step is to create or obtain a digital 3D model of the object you wish to print. This can be done using CAD software or by downloading pre-existing designs from online repositories.
2. Slicing:
Once the digital model is ready, specialized software slices it into thin cross-sectional layers, dividing the object into countless two-dimensional layers that the 3D printer can understand.
3. Printing Process:
The 3D printer reads the sliced file and begins the printing process. It starts by depositing or solidifying the chosen material layer by layer, following the instructions from the digital model. Various materials can be used, including plastics, metals, ceramics, and even biological substances.
4. Post-Processing:
After the printing is complete, the object may require additional post-processing steps such as removing support structures, polishing, or painting to achieve the desired finish. These steps vary depending on the material used and the complexity of the object.
Types of 3D Printing Techniques
1. Fused Deposition Modeling (FDM)
Fused Deposition Modeling, also known as Fused Filament Fabrication (FFF), is one of the most widely used 3D printing techniques. FDM printers utilize a thermoplastic filament that is heated to its melting point and then extruded through a nozzle. The molten plastic is deposited layer by layer, gradually building the object. FDM is known for its affordability, ease of use, and compatibility with a wide range of materials. It is commonly employed in prototyping, functional parts manufacturing, and hobbyist projects.
2. Stereolithography (SLA)
Stereolithography (SLA) was one of the earliest 3D printing techniques developed. SLA printers use a vat of liquid photopolymer resin that is selectively cured using a UV laser. The laser scans the surface of the resin, solidifying it layer by layer, following the pattern provided by a digital model. SLA offers excellent precision and surface finish, making it ideal for producing intricate and high-resolution models, prototypes, and jewelry.
3. Selective Laser Sintering (SLS)
Selective Laser Sintering (SLS) is a powder-based 3D printing technique that utilizes a high-powered laser to fuse or sinter powdered material, typically nylon or other polymers. The laser selectively fuses the particles together, layer by layer, based on the digital model. SLS does not require support structures as the surrounding powder acts as a self-supporting medium during the printing process.
This makes SLS ideal for creating complex geometries, functional prototypes, and end-use parts with excellent mechanical properties.
4. Digital Light Processing (DLP)
Digital Light Processing (DLP) is a 3D printing technique similar to SLA that uses a projector instead of a laser. The projector shines light onto a vat of liquid resin, selectively curing it layer by layer. DLP offers faster print speeds compared to SLA, as an entire layer can be exposed simultaneously. It provides high-resolution prints with smooth surface finishes, making it suitable for applications such as jewelry, dental models, and figurines.
5. Binder Jetting
Binder Jetting is an additive manufacturing technique that involves depositing a liquid binder onto a powdered material, layer by layer. The binder acts as an adhesive, bonding the particles together to form the object. After printing, the object is usually sintered or infiltrated with a secondary material to enhance its strength.
Binder Jetting is commonly used for producing sand molds and cores in foundry applications, as well as creating full-color 3D-printed objects.
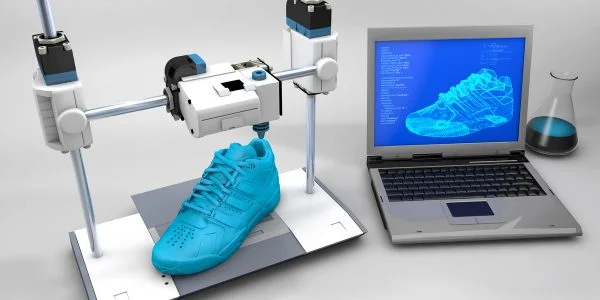
Benefits of 3D Printing in Various Industries
1. Design Flexibility and Customization
One of the key advantages of 3D printing is its unparalleled design flexibility. Traditional manufacturing techniques often have limitations in terms of design complexity and customization. However, 3D printing allows for the creation of intricate, geometrically complex designs that were previously unattainable.
This enables designers and engineers to produce highly customized and personalized products tailored to specific requirements. From unique jewelry designs to custom prosthetics and dental implants, 3D printing opens up new horizons for design possibilities.
2. Rapid Prototyping and Iteration
3D printing has revolutionized the prototyping process by significantly reducing time and costs. In the past, creating prototypes involved lengthy and expensive tooling processes. With 3D printing, designers can transform digital models into physical prototypes within hours or days, allowing for rapid iteration and refinement.
This accelerated prototyping process facilitates faster product development cycles, enabling companies to bring products to market more efficiently.
3. Cost Efficiency
Traditional manufacturing methods often involve high setup costs, especially for small production runs or customized products. 3D printing eliminates the need for expensive tooling, molds, and fixtures, making it a cost-effective alternative.
The ability to produce objects on demand and in small quantities reduces inventory costs and minimizes the risk of overproduction. Moreover, 3D printing enables the consolidation of multiple components into a single printed part, further reducing assembly costs and simplifying supply chains.
4. Waste Reduction and Sustainability
3D printing is inherently more sustainable than traditional manufacturing techniques. With traditional methods, a significant amount of material is wasted through subtractive processes. In contrast, 3D printing is an additive process, only utilizing the exact amount of material needed for the object. This minimizes material waste and reduces environmental impact.
Additionally, 3D printing enables the use of recycled materials, contributing to a more sustainable and circular economy.
5. Complex Geometries and Lightweight Structures
Another remarkable benefit of 3D printing is its ability to create complex geometries and lightweight structures. Traditional manufacturing often faces limitations in producing intricate designs and complex shapes. However, 3D printing can fabricate objects with internal cavities, overhangs, and intricate lattice structures that are not feasible through conventional methods.
This is particularly advantageous in industries such as aerospace and automotive, where lightweight and strong components are highly desirable for improved fuel efficiency and performance.
6. Personalized Healthcare Solutions
The field of healthcare has witnessed significant advancements through 3D printing. Customized medical implants, prosthetics, and surgical models can be produced to match the specific anatomical needs of patients. This level of personalization improves patient outcomes, enhances comfort, and reduces the risk of complications.
Furthermore, 3D bioprinting holds immense potential in regenerative medicine by creating living tissues and organs for transplantation, significantly advancing the field of organ transplantation.
5. Impact and Future Perspectives
The impact of 3D printing on various industries is expected to be far-reaching. It has the potential to disrupt traditional manufacturing methods, enabling decentralized production and reducing supply chain complexities. Customization and personalization will become more prevalent, as individuals can design and print objects tailored to their specific needs.
As technology advances, 3D printers are becoming more affordable, faster, and capable of utilizing a broader range of materials. This accessibility will further democratize manufacturing and foster innovation across industries, empowering individuals and small businesses to bring their ideas to life.
Also, read Jindal scholarship
Comments on “3D Printing: Exploring the Revolutionary Technology”
Comments are closed.