There are several material removal techniques that are performed using different machine tools. There are wide ranges of cutting tool materials that are used by machine tools. The different material removal techniques involved are:
• Material removal with single point metal cutting tool.
• Use of multipoint metal cutting tool for material removal.
• Abrasives as a cutting tool.
• Ultrasonic machining.
• Electrochemical machining.
• Electro discharge machining.
• Laser beam machining.
• Plasma machining.
Different machine tools have different applicability depending on the material that can be machined. The efficiency of different machine tools has increased with numerical control. However, for the operation of some machine tools, a special machining environment is required.
The machine using numerical control and the machine tools with different control systems do not differ in the actual cutting process, given that in both cases the same material removal technique is employed. This is because the numbering control is just a technique of controlling the operation of the machine tool and is not a machine tool.
The efficiency of the machining operation is improved by feeding information related to the cutting process to a control unit which can then control the relative movement between the tool and the workpiece. However, in some cases of machine tools, the numerical system cannot be linked directly to the actual cutting process.
The tool or workpiece is mounted on a table. The amount of table movement, the direction of movement and the rate at which the table must be moved is precisely and precisely controlled through a numerical control mechanism.
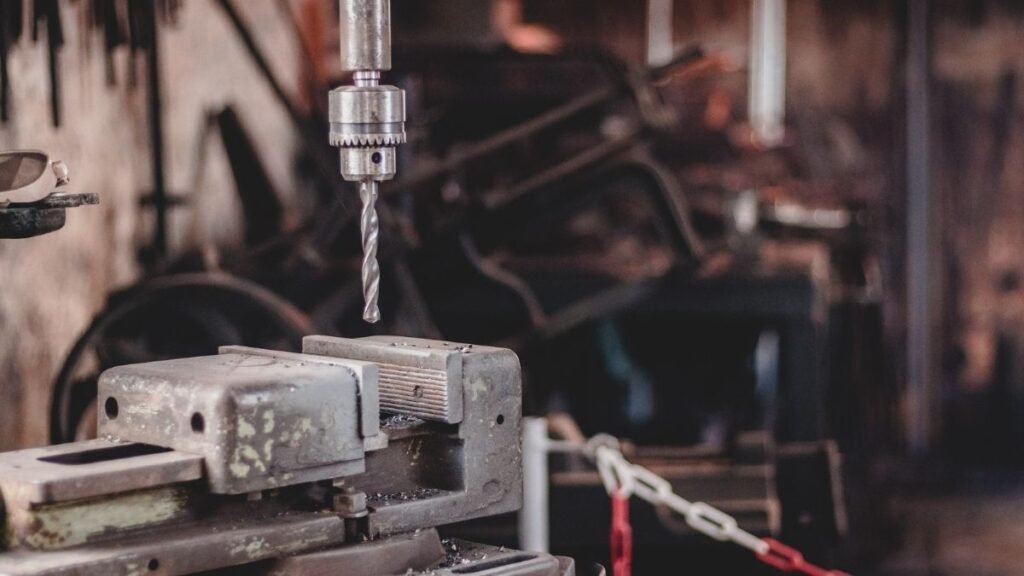
THE Numerical control also controls the other features of a machine, such as the selection of the proper cutting tool by turning the cutting fluid flow on and off and spindle speed selection. This helps in the production of products with greater accuracy and precision. Numerical control allows for a wide range of applications.
These include control plotters, oxyacetylene flame cutting machines, tower presses, inspection equipment, robot measurement and control equipment. The relative movements between the tool and the workpiece determine the type of geometry produced in the part. The three different kinematic principles used for producing the necessary geometry in a machine tool are generation, copying and forming.
The relative movement of the tool in relation to the part produces the desired shape on the workpiece. The principle of generation encompasses the production of the part parameters. The parameters are typically the solid of revolution and a straight line. These are the two main components and their combinations that make up the required shape of the component.
It is usually recommended to use these shapes as it would be difficult to control the relative position tool and workpiece movement. However, many other ways can be used with the use of numerical control techniques. For example, the generation of a cylinder occurs through a combination of circles and straight lines. There are four different ways to use this combination to generate a cylinder. One of these methods involves rotating the tool and its movement.
This method is normally used in the case of the smaller tool in relation to the workpiece. A similar technique is also adopted by vertical boring and boring machines. The second method involves rotating the workpiece with its axis movement. The method is suitable in cases where the dimensions of the workpiece are smaller than the tool. The example includes cylindrical grinding. Other the cylinder generation method involves the rotational movement of the tool and the axial axis part movement.
Comments on “Material Removal Techniques in Manufacturing Process”