Table of Contents
Introduction:
Metal cutting is an essential process in manufacturing industries that involves the removal of excess material from a workpiece to obtain a specific shape and size. In this process, a cutting tool is used to chip away at the material, resulting in chips. Chips are a byproduct of the cutting process, and their properties depend on various factors.
Types of Chips in Metal Cutting
Continuous Chips
Continuous chips are long, continuous curls that form when a cutting tool is used on a ductile material such as aluminum or copper. These chips are formed when the material being cut is subjected to shear stress along the cutting edge of the tool. Continuous chips are usually thin and narrow and have a consistent thickness throughout their length.
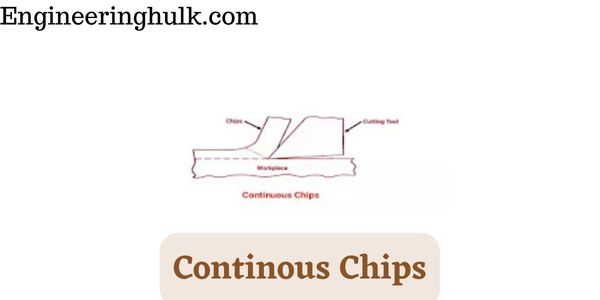
Advantages:
1 – Continuous chips are easy to manage and remove from the work area.
2 – They produce a smooth surface finish on the workpiece.
3 – Continuous chips reduce the amount of heat generated during the cutting process.
Disadvantages:
1 – Continuous chips can wrap around the cutting tool and cause tool wear.
2 – They can also create chip buildup on the cutting tool, reducing its effectiveness.
Discontinuous Chips
Discontinuous chips are formed when a cutting tool is used on a brittle material such as cast iron or hardened steel. These chips are broken into small pieces and are irregular in shape. The formation of discontinuous chips is due to the high level of stress and strain that the material experiences during the cutting process.
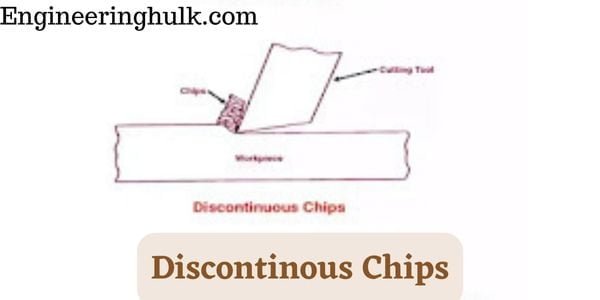
Advantages:
1 – Discontinuous chips are easy to manage and remove from the work area.
2 – They produce a rough surface finish on the workpiece, which may be desirable in certain applications.
3 – Discontinuous chips reduce the amount of heat generated during the cutting process.
Disadvantages:
1 – Discontinuous chips can cause tool wear due to their irregular shape and high level of stress.
2 – They can also create chip buildup on the cutting tool, reducing its effectiveness.
Continuous chip with Built-Up Edge
Built-up edge chips are formed when the cutting tool comes into contact with the workpiece material and adheres to it. These chips are typically larger in size and irregular in shape. The formation of built-up edge chips is due to the high level of friction between the tool and the workpiece material.
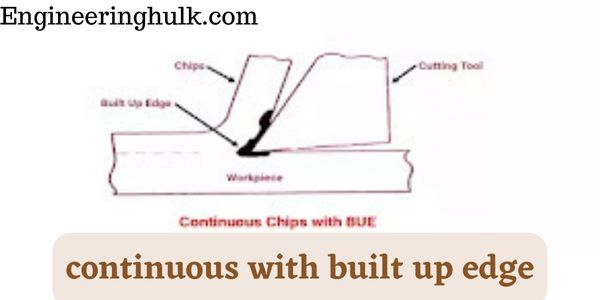
Advantages:
1 – Built-up edge chips reduce the amount of heat generated during the cutting process.
2 – They can also improve the surface finish of the workpiece in certain applications.
Disadvantages:
1 – Built-up edge chips can cause tool wear and reduce the tool’s effectiveness.
2 – They can also create surface defects on the workpiece due to their irregular shape.
Factors Affecting Chip Formation
1. Cutting Speed
The cutting speed is the speed at which the cutting tool moves across the workpiece. The higher the cutting speed, the thinner and longer the chips will be. Conversely, a lower cutting speed will result in thicker and shorter chips.
2. Feed Rate
The feed rate is the distance that the cutting tool moves into the workpiece with each pass. A higher feed rate will result in thicker and shorter chips, while a lower feed rate will produce thinner and longer chips.
3. Cutting Depth
The cutting depth is the depth at which the cutting tool penetrates into the workpiece. A higher cutting depth will result in thicker and shorter chips, while a lower cutting depth will produce thinner and longer chips.
4. Workpiece Material
The material being cut plays a significant role in chip formation. Ductile materials such as aluminum and copper tend to form continuous chips, while brittle materials such as cast iron and hardened steel tend to form discontinuous chips.
Advantages and Disadvantages of Chip Formation metal cutting
Advantages of Chips in Metal Cutting:
1. High-Speed Cutting: Chips are very effective for high-speed metal cutting because they are made of hard materials like carbide, which can withstand high temperatures and pressures. This makes them ideal for use in industries where high-speed cutting is essential.
2. Long Tool Life: Chips have a longer tool life than other cutting tools because they are made of durable materials. They are also resistant to wear and tear, making them ideal for use in applications where the tool is subjected to harsh conditions.
3. Versatility: Chips can be used for a wide range of metal cutting applications, including turning, milling, and drilling. They are also suitable for cutting a variety of materials, including steel, aluminum, and titanium.
4. Increased Productivity: The use of chips in metal cutting can increase productivity because they can cut at higher speeds and with greater precision. This can lead to faster production times, lower costs, and improved product quality.
Disadvantages of Chips in Metal Cutting:
1. High Cost: Chips are generally more expensive than other cutting tools because they are made of hard materials that are difficult to manufacture. This can make them cost-prohibitive for some applications.
2. Difficult to Sharpen: Chips are not easily sharpened, and once they become dull, they must be replaced. This can be a disadvantage for applications where frequent tool changes are necessary.
3. Chipping: While chips are designed to break off during the metal cutting process, they can sometimes chip or fracture in an uncontrolled manner, leading to damage to the workpiece or the cutting tool.
4. High Cutting Forces: Chips can generate high cutting forces, which can cause problems such as vibration, noise, and tool wear. This can be a disadvantage for applications where precision and accuracy are critical.
Also, read the volumetric strain
Comments on “Types of Chips in Metal Cutting”
Comments are closed.