Table of Contents
Ultrasonic machining (USM) is a non-conventional machining process that employs a tool vibrating at an ultrasonic frequency to remove material from a workpiece, usually hard and brittle materials like glass, ceramics, and composite materials. This process is used to produce complex or precise shapes and features that might be difficult to achieve with traditional machining techniques.
Principles of Operation
The fundamental principle of ultrasonic machining is the use of ultrasonic vibrations to machine a workpiece. Here’s how it works:
- Transducer Generation: An ultrasonic transducer converts electrical signals into mechanical vibrations at ultrasonic frequencies, typically ranging from 20 to 40 kHz.
- Amplification: The vibrations are then amplified and transferred to a tool that possesses a specific shape to match the required workpiece features.
- Abrasive Action: A slurry containing abrasive particles like silicon carbide or aluminum oxide is directed to the interface between the tool and the workpiece. The vibration of the tool forces the abrasive particles against the workpiece.
- Material Removal: The continuous impact of the abrasive particles on the workpiece’s surface erodes material in a controlled manner, enabling the tool to slowly shape the workpiece into the desired form.
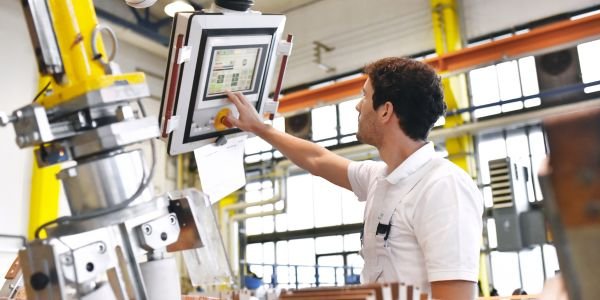
Key Components
1. Ultrasonic Transducer
The ultrasonic transducer, usually made of piezoelectric materials, generates the required vibrations. The transducer converts high-frequency electrical signals into mechanical vibrations.
2. Tool Holder and Tool
A horn or tool holder amplifies the vibrations and directs them to the cutting tool. The tool, typically made of soft material like steel, is designed to have a form that corresponds to the negative shape of the desired workpiece feature.
3. Abrasive Slurry
The slurry contains abrasive particles suspended in a liquid. This slurry is crucial for the cutting action, as the particles act as the cutting edges.
Advantages and Disadvantages
Advantages:
- Versatility: Works well with hard and brittle materials, including ceramics, glass, and semiconductors.
- Precision: Capable of producing highly complex and detailed geometries.
- Cool Operation: The lack of direct tool-to-workpiece contact means reduced heat, minimizing thermal damage.
- No Chemical Alterations: The workpiece undergoes no significant chemical alteration during machining.
Disadvantages:
- Slow Material Removal Rate: The process can be time-consuming, especially for large jobs.
- Tool Wear: The tool may suffer wear over time, which could affect precision.
- Cost: High initial cost for equipment and regular replenishment of abrasive slurry can be expensive.
Applications
Ultrasonic machining has found applications in various fields, including:
- Aerospace: For machining advanced composite materials.
- Medical Industry: To produce precise medical instruments.
- Electronics: In the fabrication of micro-electromechanical systems (MEMS) and semiconductor devices.
- Automotive Industry: For machining hard-to-machine materials like carbides.
Ultrasonic machining has evolved as an essential technique for machining hard and brittle materials that are difficult to process using conventional methods. With the correct setup, it can provide high precision and intricate details, although it comes with some limitations like a slower material removal rate and high costs.
As technology advances, we can anticipate improvements in USM that could enhance efficiency, broaden its application, and further reduce costs, ensuring that this method retains its valuable place within modern manufacturing.
Also, read Abrasive jet machining