Table of Contents
Key Takeaways
- Understanding different types of industrial pumps is critical to choosing the right one for your needs.
- Advancements in pump technology are leading to improved efficiency and more intelligent operations.
- Maintenance and eco-friendly practices are critical for sustainable and safe pump usage.
- Future trends in the industry point toward further automation and energy-saving measures.
Pumps are foundational components across a broad spectrum of industries, proving essential to the functionality of various systems. From the vast networks of wastewater management to the precision-dependent processes in chemical manufacturing, choosing industrial pumps can significantly affect efficiency, costs, and environmental footprint. This in-depth exploration into the world of pumps highlights their core importance and the innovations driving the industry forward.
Types of Industrial Pumps
Industrial pumps can be broadly classified into two categories based on their operating mechanisms: centrifugal and positive displacement pumps. Centrifugal pumps are renowned for their simplified mechanics and ability to handle a high volume of fluids, making them suitable for water supply systems, cooling systems, and irrigation. Positive displacement pumps, on the other hand, are perfect for applications requiring precise dosing or handling of viscous fluids because they are pressure-insensitive and maintain a constant flow. Beyond these, specialized pumps such as diaphragm, gear, and peristaltic pumps are tailored to meet the exacting demands of industries that deal with abrasive, corrosive, or delicate materials.
Selection Criteria for Industrial Pumps
Selecting the best industrial pump requires taking into account several important factors. The fluid characteristics, such as viscosity, temperature, and chemical composition, are essential for selecting a pump with suitable construction materials. Additionally, operational conditions like flow rate requirements, discharge pressure, and suction conditions must align with the pump’s capability. It ensures that the chosen pump will serve its purpose efficiently and stand the test of time under the given conditions.
The Impact of Technological Advances on Pump Efficiency
The relentless pursuit of enhanced efficiency and minimized operational costs has led to significant technological advancements within the pump industry. Modern industrial pumps are increasingly outfitted with variable frequency drives (VFDs), allowing speed adjustments that lead to considerable energy savings. Beyond energy conservation, current innovations have introduced smart pump systems that integrate seamlessly with automated control systems, providing real-time data for predictive maintenance and process optimization. This development holds promise for the future of industry-wide sustainability.
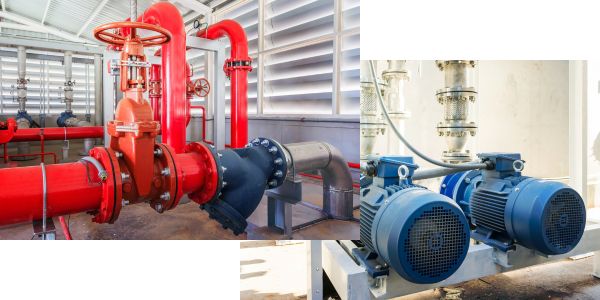
Maintenance and Troubleshooting of Industrial Pumps
Maintenance practices are paramount for ensuring the longevity and efficiency of industrial pumps. Scheduled inspections and regular upkeep, such as bearing lubrication and seal replacement, can prevent most pump failures. In cases where performance issues do arise, the ability to quickly identify and rectify problems is critical. Common issues include cavitation, seal leaks, and impeller wear, each of which offers a set of symptoms and solutions. Being well-versed in troubleshooting methods means less downtime and more productivity.
Environmental Considerations in Pump Usage
In an era where environmental impact is under the microscope, industrial pump operations are scrutinized for sustainability. Emphasizing energy-efficient designs, responsible use of resources, and minimizing emissions are vital for any industry utilizing pumping systems. By implementing eco-friendly infusions like recycling discharge fluids or optimizing pump system layouts, industries can significantly reduce the ecological impact of their operations.
Safety Measures and Compliance in Pump Operation
The safe operation of industrial pumps is non-negotiable, with strict regulations governing their use. Safety valves, overheating protection, and pressure gauges are just a few features that must comply with industry standards to prevent accidents. Regular safety training for maintenance personnel and operators ensures that those interacting with pump systems are prepared to manage risks effectively, thereby protecting human and material assets.
Case Studies: Real-World Applications of Industrial Pumps
Nothing speaks to the capabilities of industrial pumps quite like their real-world applications. Examining the use of these pumps in scenarios ranging from vast mining operations to precision-dependent pharmaceutical manufacturing reveals their adaptability and efficiency. These case studies also underscore the critical role of proper pump selection and maintenance in optimizing production and minimizing costs, offering industry professionals tangible insights into their operations.
The Future of Pump Technology
The horizon for industrial pump technology is vibrant, promising further efficiencies and more intelligent systems. Research is paving the way for applying artificial intelligence (AI) and machine learning (ML) in pump diagnostics and predictive maintenance, suggesting a future where downtime becomes increasingly rare, and systems are even more closely monitored for optimum efficiency. These innovations will likely redefine standard practices in pump selection and operation, emphasizing the importance of staying current with technological trends.
Also, read XNXP personality traits