Table of Contents
What is Lean Manufacturing?
Lean manufacturing is a production philosophy and methodology that has revolutionized the way companies approach production processes. It originated in Japan, particularly at Toyota, and has since gained global recognition for its ability to enhance efficiency, reduce waste, and improve product quality.
Lean manufacturing, often referred to simply as “lean,” is a systematic approach to eliminating waste in all forms across the entire production process. Its primary goal is to maximize value for customers while minimizing resources, time, and costs. Lean principles emphasize the continuous improvement of processes to achieve operational excellence.
Key Principles of Lean Manufacturing
- Value: Lean manufacturing begins by identifying what customers truly value in a product or service. This is often referred to as the “value stream.” Understanding customer needs helps organizations focus their efforts on delivering what matters most.
- Value Stream Mapping: This technique involves creating a visual representation of the entire production process, from raw materials to the end product. It helps identify areas of waste and inefficiency, allowing organizations to streamline their operations.
- Flow: Lean manufacturing emphasizes the smooth and continuous flow of materials and information through the production process. Reducing bottlenecks and interruptions is critical to maintaining an efficient flow.
- Pull System: Instead of pushing products through the production line, lean manufacturing uses a “pull” system, where products are produced only when there is demand. This minimizes excess inventory and reduces the risk of overproduction.
- Just-in-Time (JIT): JIT is a core concept in lean manufacturing, where materials and components are delivered to the production line exactly when they are needed, eliminating the need for extensive warehousing and reducing carrying costs.
- Takt Time: Takt time is the rate at which a product must be produced to meet customer demand. It serves as a pacing mechanism for production and helps prevent overproduction.
- Continuous Improvement (Kaizen): Lean organizations foster a culture of continuous improvement. Employees are encouraged to identify and eliminate waste, suggest process enhancements, and implement changes incrementally.
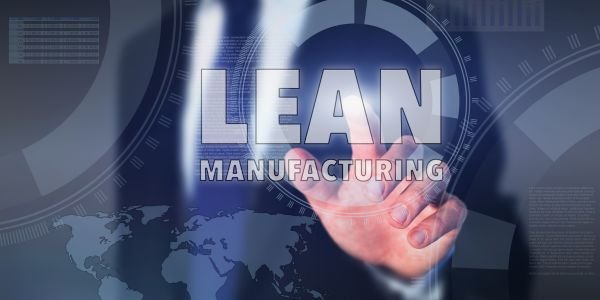
Benefits of Lean Manufacturing
Implementing lean manufacturing principles offers numerous advantages for organizations:
- Cost Reduction: By eliminating waste and optimizing processes, lean manufacturing reduces production costs, leading to higher profit margins.
- Improved Quality: Lean focuses on producing defect-free products by identifying and addressing quality issues at their source.
- Enhanced Efficiency: Streamlining processes and reducing downtime leads to improved operational efficiency and resource utilization.
- Faster Delivery Times: JIT and efficient flow systems reduce lead times, allowing companies to respond more quickly to changing customer demands.
- Increased Flexibility: Lean manufacturing makes it easier for companies to adapt to market changes and fluctuations in demand.
- Empowered Workforce: Encouraging employees to actively participate in process improvement boosts morale and engagement.
- Sustainable Practices: Reducing waste and conserving resources aligns with sustainable and environmentally friendly business practices.
Challenges of Implementing Lean Manufacturing
While lean manufacturing offers numerous benefits, its implementation can be challenging:
- Cultural Shift: Adopting a lean culture requires a significant change in mindset and workplace behavior, which can be met with resistance.
- Initial Investment: Transitioning to lean may require upfront investments in training, technology, and process changes.
- Complexity: Balancing the various lean principles and tools can be complex, and organizations must tailor their approach to their specific needs.
- Continuous Commitment: Maintaining lean practices requires ongoing dedication and vigilance to sustain improvements over time.
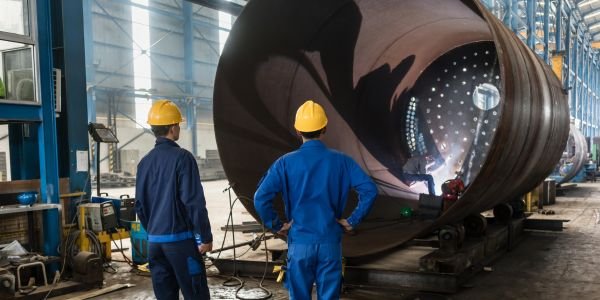
Five Lean Principles
Lean manufacturing is based on several core principles aimed at improving efficiency, reducing waste, and enhancing overall productivity. Five fundamental principles of lean manufacturing are:
- Value-Added Focus: The primary focus of lean manufacturing is to identify and deliver value to the customer. Anything that does not directly contribute to the product’s value from the customer’s perspective is considered waste and should be minimized or eliminated. This principle emphasizes the importance of understanding customer needs and aligning all processes with those needs.
- Identify and Eliminate Waste (Muda): Waste in manufacturing can take various forms, including overproduction, excess inventory, unnecessary motion, defects, waiting time, and more. Lean manufacturing aims to identify and eliminate these forms of waste through continuous improvement efforts. The seven types of waste often referenced in lean are overproduction, inventory, waiting, motion, transportation, defects, and over-processing.
- Continuous Flow (JIT Production): Lean manufacturing promotes the concept of continuous flow production, where products move through the production process without interruption or delays. This is often achieved through practices like just-in-time (JIT) production and single-piece flow, which minimize work-in-progress and reduce the time between process steps.
- Pull Systems: Instead of pushing products through the production process based on a schedule, lean manufacturing uses pull systems where production is initiated based on customer demand. This prevents overproduction and minimizes inventory while ensuring that items are produced only when needed.
- Empowerment and Respect for People: Lean manufacturing recognizes that employees are a valuable source of knowledge and innovation. It emphasizes the importance of empowering and involving employees in decision-making, problem-solving, and continuous improvement efforts. Creating a culture of respect for people fosters employee engagement and a sense of ownership in the process.
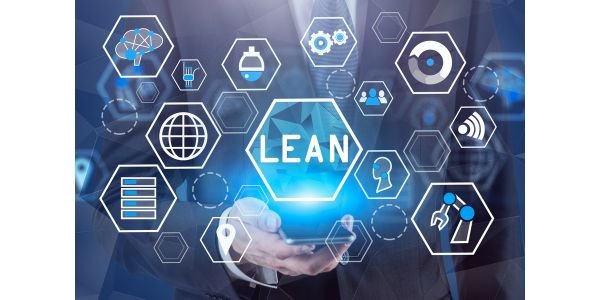
Lean Manufacturing Examples
Lean manufacturing is a production practice that considers the expenditure of resources in any aspect other than the direct creation of value for the end customer to be wasteful and thus a target for elimination. Lean manufacturing principles aim to reduce waste, increase efficiency, and improve overall product quality. Here are some examples of lean manufacturing principles and practices in action:
- Just-In-Time (JIT) Inventory: JIT is a key principle of lean manufacturing, where materials and components are ordered and received just in time for production, minimizing inventory carrying costs and reducing waste.
- Kanban System: The Kanban system uses visual signals to trigger the replenishment of materials or components as they are consumed in the production process. This ensures that inventory levels are maintained at an optimal level without overproduction.
- 5S System: The 5S system focuses on workplace organization and cleanliness. The five S’s stand for Sort, Set in order, Shine, Standardize, and Sustain. This helps create an organized and efficient workspace.
- Single-Piece Flow: Instead of producing items in large batches, lean manufacturing often promotes single-piece flow or small-batch production. This reduces work-in-progress inventory and improves the ability to respond to customer demand changes.
- Value Stream Mapping: Value stream mapping is a visual tool used to analyze and improve the flow of materials and information through the production process. It helps identify areas of waste and opportunities for improvement.
- Poka-Yoke (Error-Proofing): Implementing mistake-proofing mechanisms to prevent defects and errors in the production process, reducing the need for rework and ensuring higher product quality.
- Continuous Improvement (Kaizen): Kaizen is the practice of continuously seeking and implementing small, incremental improvements in processes. It involves employees at all levels in identifying and solving problems.
- Andon Systems: Andon systems use visual signals to alert workers and supervisors to production problems or abnormalities. This helps in quick response and resolution of issues.
- Cross-Training: Cross-training employees to perform multiple tasks within a production process ensures flexibility in resource allocation and reduces reliance on specialized workers.
- Standard Work: Developing and following standardized work procedures to ensure consistency and efficiency in production processes. This helps reduce variability and waste.
- Total Productive Maintenance (TPM): TPM focuses on proactive maintenance to prevent equipment breakdowns, improve equipment efficiency, and reduce downtime.
- KPI Monitoring: Regularly monitoring key performance indicators (KPIs) such as cycle time, defect rate, and productivity to identify areas for improvement and track progress.
- Supplier Collaboration: Collaborating closely with suppliers to ensure a steady and high-quality supply of materials, reducing the risk of disruptions.
- Pull Systems: In a pull system, production is based on customer demand rather than pushing products through the system. This minimizes overproduction and waste.
- Visual Management: The use of visual cues, such as charts, graphs, and color-coding, to provide real-time information about production status, making it easier for employees to understand and respond to changes.
Lean manufacturing is a powerful methodology that has transformed the way organizations approach production processes. By focusing on value, waste reduction, and continuous improvement, companies can achieve higher efficiency, superior product quality, and greater customer satisfaction.
While implementing lean may present challenges, the long-term benefits are well worth the effort, making it a valuable strategy for businesses across industries seeking to thrive in today’s competitive markets.
Also, read Stick Welding
Comment on “Lean Manufacturing: Production for Efficiency & Quality”
Comments are closed.