Table of Contents
What is plain cement concrete (PCC) in foundation construction?
Concrete has been used for many wonderful things throughout history, for architecture, infrastructure, and much more.
The term PCC stands for plain cement concrete. The mixture of cement, fine aggregate (sand), and coarse aggregate is generally referred to as plain cement concrete (PCC).
Before beginning any RCC or masonry work directly into the excavated soil, PCC is performed to form a level surface and avoid pouring concrete directly into the soil to prevent it from mixing with the soil and also to prevent the soil from drawing water out of the soil. I usually. CCP, weakening it.
Plain cement concrete may also be simply called “cement concrete (CC)” or “bonding concrete”. Some even call it a “mud rug.”
Making concrete is not easy. It has 4/5 main ingredients.
• Cement
• Sand
• Coarse aggregate
• Water
• Mixture
Plain cement concrete
• As a concrete bed under wall footings, column footings and in walls under beams.
• As sill concrete for a hard, smooth surface on window sills and vents.
• With regard to the finishing concrete for the parapet and mixed walls.
• To mark the area around buildings.
• Make floors.
• To make tennis courts, basketball courts, etc.
• Baseboard protection
Plain cement concrete? Uses and training method.
The purpose of plain cement concrete, also known as PCC, is to provide a firm, impervious bed to RCC in the foundation, where the soil is soft and malleable. It is mainly applied on flat brick soles or without flat brick soles.
When reinforcement is not used inside the concrete, it is defined as plain cement concrete. It’s just a mixture of concrete ingredients.
Characteristics of Plain Cement Concrete – Below is some vital characteristics of plain cement concrete:
Compressive strength: 200 to 500 kilograms/square centimeter
Tensile strength: 50 to 100 kilograms/square centimeter
🇧🇷 Density: 2200 to 2500 kilograms/cubic meter
🇧🇷 Stability: Excellent
Plain Cement Concrete Applications: PCC is found primarily in concrete foundations, slabs, and walkways. Where the underlying soil is weak and flexible, a flat brick sole is provided under the PCC.
To form PCC, the following materials are used:-
Cement: Normally, Portland cement is used as the bonding material in PCC.
Fine aggregate: Sand is used as fine aggregate. The fineness modulus (FM) of the sand should be between 1.2 and 1.5. FM represents an index number that demonstrates the average size of particles in sand. Semi performing a sieve analysis.
Coarse Aggregate – Usually, brick chips are used to develop PCC. It is also possible to use stone chips under these conditions. The coarse aggregate size remains 20 mm below.
Water: Pure potable water must be provided at the CCP.
How to build PPC?
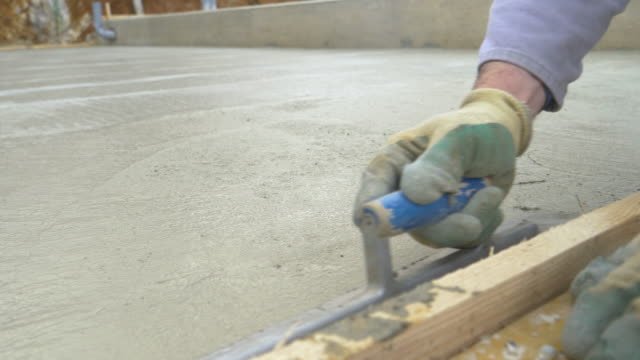
With the following methods, single cement concrete is formed.
The following tools are used for PCC production
Wooden or steel tamper
Mixing machine (if any)
PCC Thickness: PCC thickness is normally 50mm in flat brick sole (BFS). If you don’t use BFS below PCC, the thickness should be 75mm. When the PCC is used in a parking area, the thickness should be 75mm over the BFS.
Ratio of materials in the PCC: The ratio of cement, sand and brick chips in the foundation or basement should be 1:3:6. But if it is applied in the parking area, the aspect ratio will change to 1:2:4.
The production method for PCC: If ready-mix concrete is applied, this step should be skipped. If PCC is produced via mixing machine, click? How to mix concrete by mixing machine? If the concrete is mixed by hand, do you get help by clicking this link? How to mix concrete by hand?
PCC Placement and Compression:
Make sure the base level of the sand/brick bed is perfect for the PCC.
Create formwork for PCC with wooden planks according to the stipulated dimensions.
There must be no dust or foreign material in the concreting area.
The PCC bed must be covered with polyethylene.
Create level fresh concrete piers in the area with adequate spacing but not exceeding 2m of free coverage on each side.
Place the concrete gently on one side. Apply mixed concrete within 45 minutes of adding water.
To compact and finish the PCC, a wood compactor should be used.
The PCC surface must be roughened to match future jobs before the concrete solidifies.
Specifications for Single Cement Concrete (PCC)
Cement
Portland Pozzolana Cement (P.P.C) is typically used for plain cement concrete. It must comply with specifications and tests.
Sand
The sand to be used for concrete work must be clean, well-graded, hard, strong, and durable and must meet the specified requirements for its use. Add The aggregate must be of inert and clean material, dense, hard, solid, durable, non-absorbent, and capable of developing a good bond with the mortar.
coarse aggregate
The aggregate size used for PCC ranges from 10-12mm to 40mm, depending on where they will be used.
If the aggregate size is larger, it results in reduced cement consumption.
Coarse aggregate should be clean and free of elongated, flaky, or rolled pieces.
It must be free of adherent layers, lumps of clay, coal residues, clinker, slag, alkalis, mica, organic matter or other substances.
The coarse aggregate should be hard, broken granite or similar stone, free of dust, dirt and other foreign matter. The smallest stone size is 6.3 mm. All course material must be retained in a 1/4″ square mesh and must be well levelled so that the void does not exceed 42%.
Fine aggregate
Fine aggregate should be coarse sand consisting of hard, sharp, angular grains and passed through a 4.75mm square mesh screen.
Sand for PCC work must be clean and free of dust, dirt and organic matter or in accordance with standard specifications. He never used sea sand in foundation work.
Water
The water must be clean and free of alkali and the substances must be suitable for drinking.To maintain the required consistency and control the addition of water, the slump test should be performed regularly. A drop of 7.5 cm to 10 cm may be allowed for foundation work.
Mixing machine:
Rock ballast, sand and cement will be poured/mixed into one mixer to maintain the necessary proportions. Machine mixing is always preferred but in unavoidable circumstances hand mixing can be done but all quality checks must be ensured.
Formwork:
Form centering and formwork must be provided to standard specifications prior to pouring concrete to confine the support or hold the concrete in position. To prevent the concrete from sticking, the inner surface of the form must be lubricated.
PCC Mixing Methods
1. Ready Concrete
In India, concrete is traditionally produced on site, usually through the use of hand labour. However, due to the advantages of premixed concrete in modern times, its use has started to increase rapidly.
This method can speed up the build process. In addition, it can be easily performed in busy areas, at night on concreting works, on large construction sites, etc.
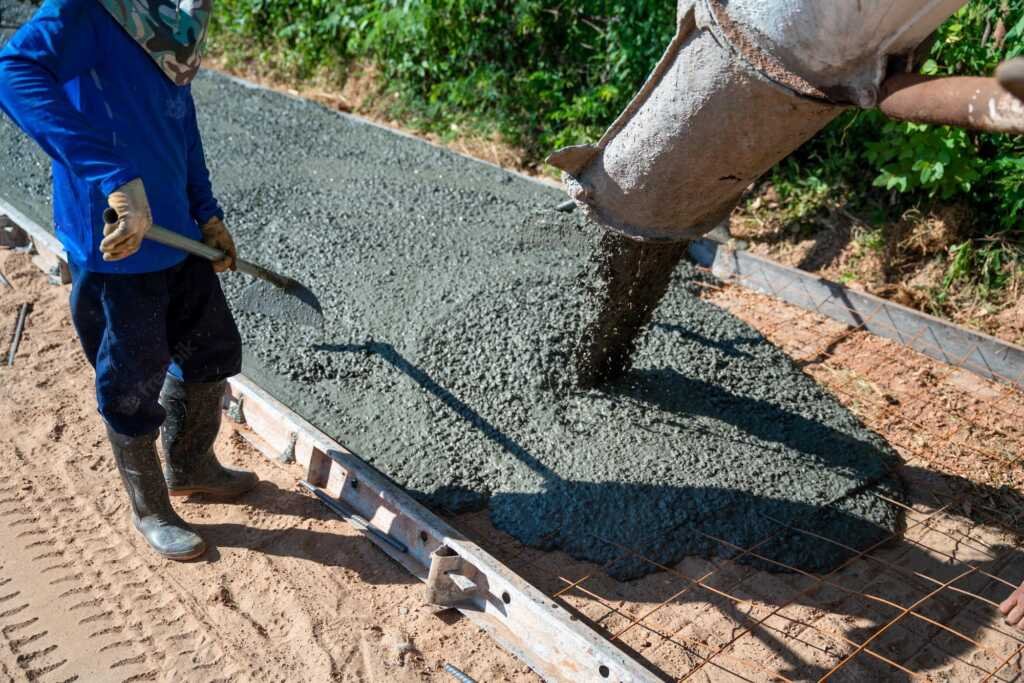
Premixed concrete is especially used in dense areas or in road construction. Very useful when you do not have adequate space for the plant and there is no space to store concrete components.
High quality concrete can be obtained with this method. Because the concrete for this type of concrete is produced using a mechanized batching plant.
In pre-mixed concrete, it is able to control the water/cement ratio in concrete compared to other types of mixing methods.
Using pre-mixed concrete helps to speed up construction and maintain proper concrete quality.
2. Hand mixing
In the manual mixing process, it is very difficult to mix the concrete components correctly. Mixing concrete by hand is only used for small works. In addition, the manual mixing process can be carried out when the demand for concrete is low and the quality control is low.
No machinery is needed for this type of mixing. Achieving the correct mix of concrete through the hand mixing process is difficult and requires great stamina.
Manual concrete mixing process
Various components of the concrete are mixed by hand in the tray as a rigid, clean and non-porous base.
A measured amount of sand and aggregate is spread on the tray.
The mixing process continues until the concrete components reach the same color and consistency in the dry state. The last amount of water is then added to the dry concrete mix.
3. Cure method
• After two hours of concreting, when the concrete has started to harden, it will be kept moist by covering it with damp jute bags for 24 hours.
• After 24 hours of placing the PCC, keep the surface of the concrete moist, flooding it with water or covering it with damp jute bags.
• PCC curing can be done by pouring water from buckets or pipes.
• Curing must be done for a minimum of 14 days.
A Strength holds of the PCC.
PCC is best known for its compressive strength. This is because PCC is much stronger in compression than in tension and is therefore, often used in compression. The ACI concrete codes provide some basic rules for converting compressive strength into tensile and flexural strength.
Compressive strength is most often measured by forming test cylinders 150 mm in diameter and 300 mm in length (6 inches in diameter, 12 inches in length) and then breaking them at a specified age (typically 28 days), although it can be performed on samples of different sizes. And origins (such as field cores or remnants from a bending test).
Some state agencies use compressive strength as a field quality assurance measure of a flexural strength specification. Flexural strength is first correlated with compressive strength based on mix design test results.
Using this correlation, QA field testing can then use the easier and more well-known compressive strength test, which can be converted back to flexural strength via previously determined correlations.
The PCC strength is defined as the compressive strength after 28 days, expressed as M15, M20, where M stands for Mix and 15 represents the compressive strength of 15 N/mm2 at 28 days.
The ratios of materials (cement, sand, coarse aggregate) to the nominal mix/design concrete normally used are 1:3:6 or 1:4:8. Since strength is not an important criterion, mixing designs is generally avoided.
Do’s and Don’ts at PCC Works
Do’s
• Check and obtain approval of the soil strata by the structural consultant before carrying out the CCP on the foundation.
• PCC formwork must be the exact size and thickness
• Dry materials must be mixed evenly before adding water.
• The water must be mixed with a bucket, in a measured amount, according to the w/c ratio (water/cement).
• Use the chute or additional labour to pour concrete where the depth is greatest.
• Remove any loose material from the sides of the pit so that no soil or other material falls into the pit during pouring.
• If the water table is high, drainage should be done at the same time as the concrete is placed.
• Compact and level the concrete correctly.
• Maintain PCC levels.
• The next day, mark the center of the column.
Don’ts
• Do not mix materials on bare ground.
• It is not enough to pour water on materials through a pipe. that is, without any measurement control.
• Do not pour concrete without levelling and compacting.
• Do not pour concrete into the pit from a height greater than 1.5 m.
• Do not allow additional cement mortar in the PCC. for a smooth finish.
Advantages of Placing Simple Cement Concrete
• The necessary cover for the lower reinforcement is ensured since the cover blocks rest on firm PCC.
• The effective depth of RCC members is achieved because the forms can be easily, uniformly, and robustly fastened, resulting in better dimensional accuracy of the RCC member of the foundation.
• The reinforcing steel bars placed in the PCC are never in contact with the soil, which can be chemically active and lead to steel corrosion in the immediate future.
• Ease of placement of steel cages and greater productivity.
• Concrete does not adhere to the ground (clay); PCC acts as a soil barrier and adheres well to overlying structural grade concrete.
Also, read Diploma in Civil Engineering
Comment on “What is plain cement concrete (PCC) in foundation construction?”
Comments are closed.