Table of Contents
Automobile Suspension System
Road Irregularities:
1. Daily use of road infrastructure, continual changes in weather conditions, and vehicle overweight will produce different wear patterns of the road surface.
2. Furthermore, a poor road construction process will eventually lead to uneven road surfaces.
3. Almost 20% of accidents are caused by the state of the infrastructure.
4. Potholes, cracks in the road, unevenness, and different levels of friction can promote emergency manoeuvring accidents.
Need for suspension System:
1. To absorb shocks and vibrations caused by irregularities in the road.
2. To transmit the load of the vehicle to the wheels (bearing the weight)
3. To maintain the stability of the vehicle (contact of the wheels with the ground)
4. To provide cushioning and ride comfort to passengers
5. To prevent body squat and body dip
Automobile Suspension System functions:
1. Protect passengers and goods from shocks on the road.
2. To preserve the stability of moving vehicles (pitch or roll)
3. Allow the wheels to always be in contact with the road when cornering and braking.
4. To maintain proper steering geometry
5. To provide adequate driving and damping properties.
6. Allow fast cornering without extreme body roll
7. To avoid an excessive body squat or an excessive body dive.
Automobile Suspension system requirements:
1. There should be minimal deflection.
2. It must have a low initial cost.
3. It must have a minimum weight.
4. It must have a low cost of maintenance and operation.
5. Must have minimal tire wear.
Basic suspension movements:
1. Rebound: The vertical movement of the whole body.
2. Pitch: The rotational movement of all parts between the spring and the road and the weight part of the spring itself.
3. Rolling: The movement on the longitudinal axis produced by centrifugal force during cornering.
Sprung and unsprung masses:
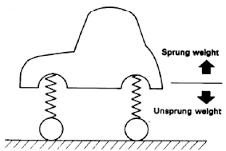
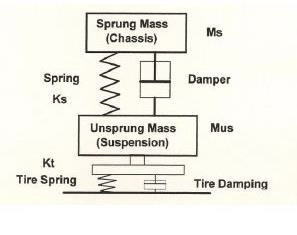
Sprung mass in Suspension System:
• In a vehicle with suspension, such as a car, motorcycle, or tank, the suspended mass (or suspended weight) is the part of the total mass of the vehicle that is supported by the suspension.
• Suspended weight generally includes body, frame, and internal components, passengers, and cargo, but does not include the mass of components suspended below suspension components (including wheels, wheel bearings, brake rotors, calipers).
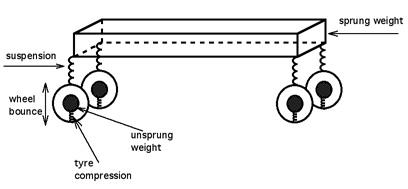
Unsprung mass in Suspension System :
1. In a suspended land vehicle, the unsprung weight (or the unsprung mass) is the mass of the suspension, wheels or tracks (as applicable) and other components directly connected to them, rather than supported by the suspension.
2. Unsprung weight includes the mass of components such as wheel axles, wheel bearings, wheel hubs, tires, and a portion of the weight of driveshafts, springs, shock absorbers and suspension links.
Types of suspension Systems:
TYPES OF SUSPENSION SYSTEM
SPRINGS
1. Steel springs
Leaf spring
Tapered leaf spring
Coil spring
Torsion bar
2. Rubber springs
Compression spring
Compression-shear spring
Steel-reinforced spring
Progressive spring
Face-shear spring
Torsional shear spring
SHOCK ABSORBERS
Telescopic
Lever arm type
INDEPENDENT SUSPENSION
FRONT-WHEEL(DEAD)
Wishbone or parallel link type
Mac-Pherson strut-type
Vertical guide type
Trailing link type
Swinging half-axle type
AIR OR PNEUMATIC SUSPENSION
AIR SPRING
Bellow type
Piston type
HYDROLASTIC SUSPENSION
STABILIZER OR
ANTI-ROLL BAR
1. The rigid / non-independent suspension has the right and left wheel attached to the same solid axle. When one wheel hits a bump in the road, its upward movement causes the other wheel to lean slightly.
2. Independent suspension allows one wheel to move up and down with minimal effect on the other.

Automobile Suspension system components:
1. Springs, which neutralize shocks from the road surface (energy storage)
2. Shock absorbers, which act to improve comfort by limiting the free oscillation of the springs. (Power dissipation)
3. Stabilizer (stabilizer bar or stabilizer bar), which prevents the side swaying of the car.
4. An articulation system, which acts to hold the previous components in place and control the longitudinal and lateral movements of the wheels.
Leaf springs:-
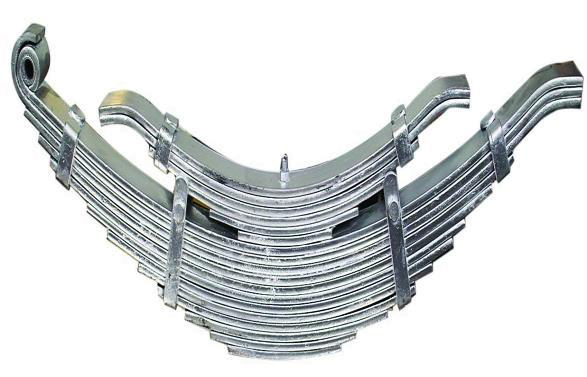
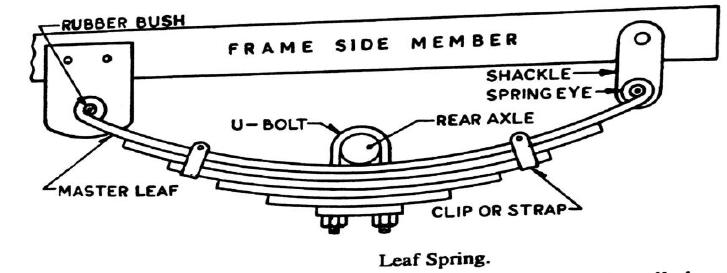
1. The Leaf springs were invented by Obadiah Elliot of London in the 18th century. He simply stacked one steel plate on top of another, pinned them down and chained each end to a carriage, it was the first Leaf springs used in a vehicle.
2. Originally called a laminated or carriage spring, it is sometimes called a semi-elliptical or carriage spring. Leaf springs are formed by bending.
3. They are made of long strips of steel.
4. Each strip is called a Sheet.
5. The long blade is called the Master Blade and consists of eyes at both ends.
6. One end is attached to the chassis frame, the other end is attached to the spring of the shackle.
7. The spring will elongate during expansion and shorten during compression.
8. This change in spring length is compensated for by the shackle.
9. The U-bolt and clamps are in the middle position of the spring.
10. Bronze or rubber bushings are provided on both eyes of the master blade.
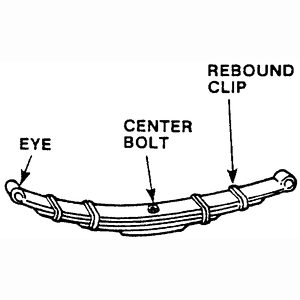
Types of Leaf Spring:
There are six types of Leaf Springs.
1. Full-elliptical type
2. Semi-elliptical type
3. Fourth – elliptical type
4. Three quarters – elliptical type
5. Cross-spring type
6. Type of auxiliary spring

Leaf springs features
- The Leaf spring acts as a link to hold the axle in position and therefore no separate links are necessary. Makes suspension construction simple and strong.
- Since the positioning of the axis is carried out by means of leaf springs, it is disadvantageous to use soft springs, ie a spring with a low spring constant.
- Therefore, this type of suspension does not provide good driving comfort.
- Leaf friction between leaf springs affects driving comfort.
- Acceleration and braking torque cause jerks and vibrations. The rope also causes back squats and nosedive jumps.
Helical springs:
- The coil springs are made of special steel for round springs wrapped in a helix shape.
- The strength and handling characteristics of a coil spring depend on the following.
1. Coil diameter
2. Number of coils
3. Spring height
4. Diameter of the steel coil that forms the spring.
The larger the diameter of the steel, the more “stiff” the spring will be. The lower the height of the spring, the stiffer the spring will be. The less you turn, the stiffer the spring is. Coil springs are primarily used with independent suspension, although they have also been used in conventional rigid axle suspension as they can accommodate well in tight spaces.
5. The energy stored per unit volume is almost double in the case of coil springs than in leaf springs.
6. Coil springs have no noise problem or static friction.
7. Coil springs can withstand bending and shear stress.
8. However, coil springs cannot withstand torque reaction and lateral thrust, for which alternative arrangements must be provided.
9. Sometimes an auxiliary coil spring is also used to provide progressive stiffness against increasing loads.
Rubber springs
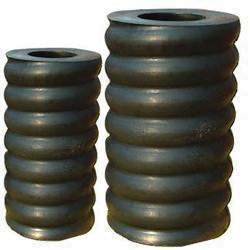
1. Since rubber can store more energy per unit mass than any other type of spring material, considerable weight can be saved with rubber suspension.
2. It is more compact than other springs.
3. It also has excellent vibration damping properties.
4. One more advantage of using rubber is that it does not fail suddenly like steel, so there is less risk.
5. First introduced in 1958 by Eric Moulton.
6. The spring is installed between the frame and the upper link of the suspension system.
7. When the spring is connected to a point near the pivot of the link, the deflection of the spring is minimized, without affecting the total movement of the wheel.
8. This spring arrangement provides a rate-of-rise characteristic, which is “soft” for small wheel movements, but becomes stiffer as the spring deflects.
9. The energy released by the rubber spring after deflection is considerably less than what is imparted to it.
10. This internal loss of energy is called hysteresis, which is an advantage because lower resistance dampers can be used.
11. Some rubber suspension systems tend to “settle” or “slide” during the initial stages of service, therefore this must be considered.
Torsion bars:
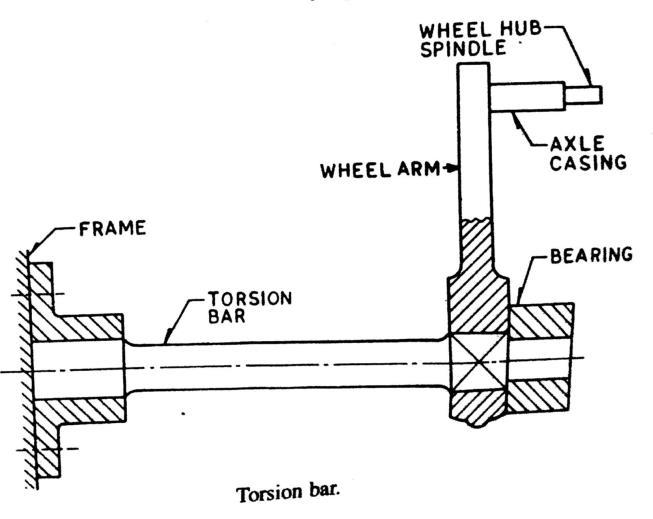
1. This is a straight bar of circular or square section attached to the frame at one end, and a lever or fork-shaped member connects its other end to the wheel. A torsion bar suspension system used in an automobile is illustrated in Fig.
2. The diameter is increased at each end of the bar and the bar is connected to the levers by splines. Provision for adjustment is made at the end of the frame to “level” the suspension.
3. Since the coil spring is a form of the torsion bar, the speed of both springs depends on the length and diameter. The speed decreases or the spring becomes softer as the length is increased or the diameter is decreased.
Advantages of Torsion Bar
• Lightweight.
• Requires less space.
• Its maintenance cost is lower.
• The initial cost is lower.
• Driving comfort is more.
Disadvantages of Torsion Bar
• Needs no acceleration or braking thrust, so additional links are required
• Lack of friction damping
Types of independent suspension systems
1. Double wishbone suspension
2. Mac-Pherson strut-type
3. Vertical guide suspension
4. Drag link suspension
5. Oscillating half-axle suspension
Double wishbone suspension System
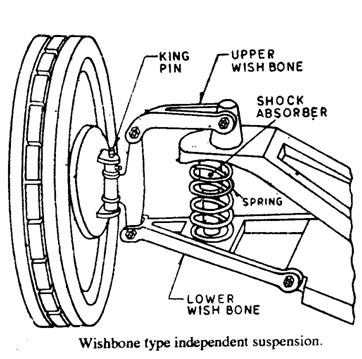
- It is the most common type of independent suspension system.
- The use of coil springs with a shock absorber on the front axle is common in this type of suspension.
- The upper and lower fork arms rotate towards the frame member.
- The spring is placed between the lower fork and the bottom of the cross member.
- The weight of the vehicle is transmitted from the body and the cross member to the coil spring through which it passes to the lower fork member.
- The damper is placed inside the coil spring and is attached to the cross member and the lower fork member.
- The swing arms not only position the wheels and transmit the vehicle load to the springs, but also resist acceleration, braking and cornering or lateral forces.
- The upper fork legs are generally kept shorter than the lower ones to keep the wheel trajectory constant and thus avoid excessive tire wear.
- However, there is a small change in tilt angle with such an arrangement.
- A short and long arm (SLA) suspension is also known as an unequal length double wishbone suspension.
- The upper-link is typically an A-arm and is shorter than the lower link, which is an A-arm or an L-arm, or sometimes a pair of tension/compression arms.
- The four-bar linkage mechanism formed by the unequal lengths of the arms causes a change in the lean of the vehicle as it rolls, helping to keep the contact patch square to the ground, increasing the maximum turning ability of the vehicle. It also reduces wear on the outer edge of the tire.
Mac-Pherson strut-type Suspension System
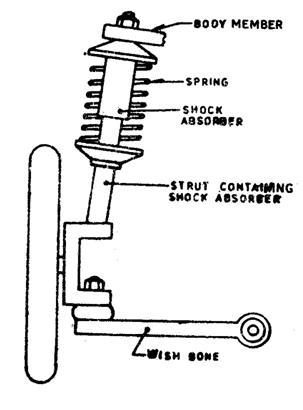
- The MacPherson strut, named after Earle S. MacPherson, who developed the suspension design in the late 1940s and patented it in 1953, is the most widely used type.
- In this design, only the lower fork is used.
- A strut containing a shock absorber and the coil spring also carries the stub axle on which the wheel is mounted.
- The fork is articulated to the cross member and positions the wheel, as well as taking acceleration, braking and lateral forces.
- This system is of simpler construction
- The lean angle does not tend to change when the wheel is moved up and down.
- This system will provide the maximum space in the engine compartment and is therefore commonly used in front-wheel-drive cars.
- This stabilizer bar system provides greater safety on the road, improves driving comfort, has a light and self-stabilizing steering.
Vertical guide suspension
- In this suspension, the kingpin is directly attached to the frame cross member.
- It can slide up and down as shown in correspondence with the movement of the wheel and therefore compresses or lengthens the springs.
- In this type, the wheel path, wheelbase and wheel altitude remain unchanged.
- But the system has the disadvantage of less stability.
Swing Arm Suspension:
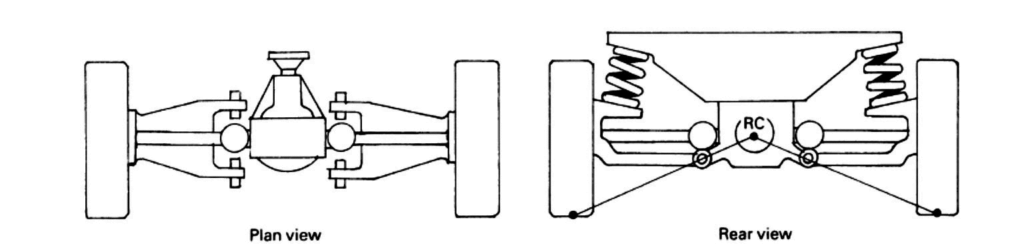
- In this type of suspension, the wheels are rigidly mounted on the transverse triangular fork A, which pivots at its ends to the chassis member in the center of the car.
- Coil springs and shock absorbers are mounted on top of the swing arm members near the outer ends.
- It is very simple to construct, but the main disadvantage is that the up-and-down movement of the wheel causes the lean angle to vary.
- Each driveshaft has a UJ mounted inside with its center aligned with that of the swingarm. Any increase in static load causes the swingarm to sag, which causes negative wheel camber and also changes the track width of the wheels.
- During cornering, the inner and outer wheels curve negatively and positively, respectively.
4. Trailing-arm / link suspension

A trailing arm suspension sometimes referred to as a trailing link, is a vehicle suspension design in which one or more arms (or “links”) are connected between (and perpendicular to and in front of) the axle and a point of pivot (located in the chassis of a motor vehicle).
Typically used on the rear axle of a motor vehicle. Trailing arm designs in live axle configurations often use just two or three links and a rigid Pan rod to locate the wheel laterally.
A trailing arm design can also be used in an independent suspension arrangement. Each wheel hub is located only by a large, roughly triangular arm that rotates at one point, ahead of the wheel. Viewed from the side, this arm is roughly parallel to the ground, and the angle changes depending on the unevenness of the road.
A semi-trailer arm suspension is a flexible, independent rear suspension system for cars in which each wheel hub is located only by a large, roughly triangular arm that rotates at two points.
Viewed from above, the line formed by the two pivots is somewhere between parallel and perpendicular to the longitudinal axis of the car; it is generally parallel to the ground. Trailing arm and multi-link suspension designs are much more commonly used for the rear wheels of a vehicle where they can allow for a flatter floor and more cargo space.
Multi-link suspension:
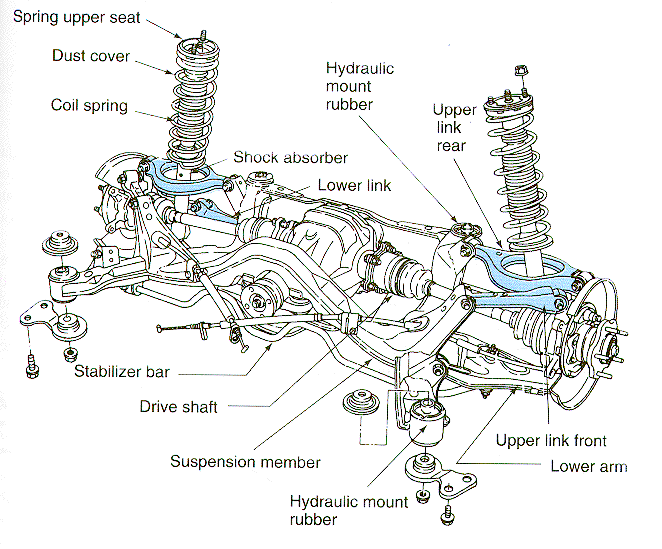
A multi-link suspension is a type of vehicle suspension design that is typically used on independent suspensions, using three or more lateral arms and one or more longitudinal arms. These arms do not have to be the same length and can be angled in the opposite direction from your “obvious” direction.
Each arm typically has a ball joint (ball joint) or rubber bushing at each end. Consequently, they react on loads along their own length, in tension and compression, but not in bending.
Some multi-links use a towing arm or wishbone, which has two bushings at one end. In a front suspension, one of the side arms is replaced by the tie rod, which connects the rack or steering box to the wheel hub. The multi-link suspension allows the car designer the ability to incorporate both good ride quality and good car handling in the same vehicle.
Anti-Roll Bar or Stabilizer Bar or Sway Bar:

When a vehicle goes over a pothole, one wheel may drift more than the other and there will be a tendency for the vehicle to roll. To reduce this tendency a stabilizer or stabilizer bar in the form of a torsion bar is used. The ends of the stabilizer are connected to the rear leaf springs or the lower forks and are supported by two bearings, which are fixed to the frame rails.
By this arrangement, when one road wheel spring deflects the other, the energy that would have caused the rocking of the vehicle is converted into the torsion of the torsion bar.
Hydroelastic suspension:
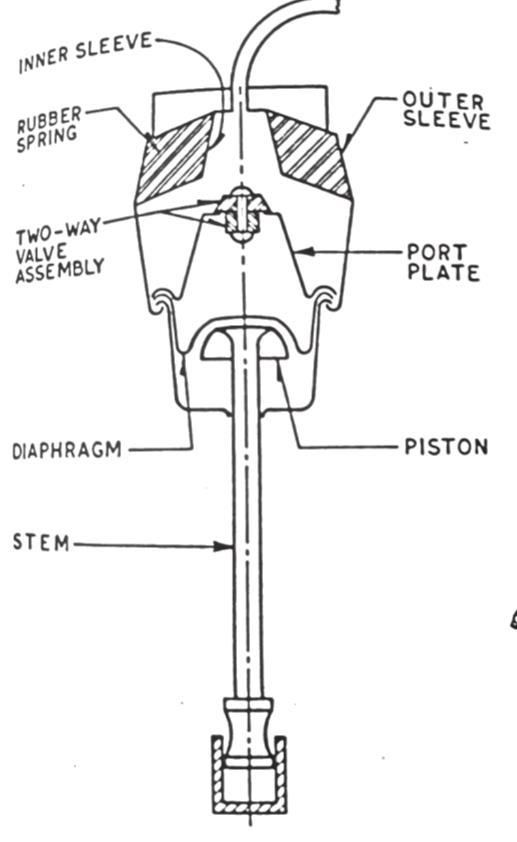
In this system, a shift unit is installed on each of the four wheels. The displacement units are interconnected by means of fluid. In the displacement unit, the rubber is used as a spring, while the fluid under pressure acts as a damping medium. The stem is connected to the wheel by means of a suitable linkage so that its movement is proportional to the up and down movement of the wheel.
This suspension is intended to improve the vehicle’s resistance to pitching, the tendency of the body to rock back and forth when the front springs are compressed and the rear springs are simultaneously expanded. The continuous forward and backward pitching motion provides a very uncomfortable ride, which can become severe when the vibration frequency of the front and rear springs is the same.
The interconnection is made by two pipes. One tube connects the units on the left side and the other on the right side. The system is pressurized with an antifreeze fluid after removing the air.
Each displacer unit contains a rubber spring; metal spacer member, holding two-way rubber damping valves; rubber diaphragm attached to the suspension linkage, which holds the wheel; and a metal body, which is fixed to the frame of the vehicle. A sudden upward movement of the front wheel causes the diaphragm to move fluid through the shock absorber.
This action, in turn, forces the fluid along the tube toward the rear unit, where it moves the diaphragm and raises the rear of the car to level with the front. When the front wheel is lowered, the fluid returns and the vehicle returns to its normal driving position.
During this sequence, the liquid has to pass through the damping valve in each unit, and the restriction to the flow of liquid in the valves and in the pipes dampens the tendency to oscillate the tone.
When a vehicle takes a curve, the vehicle body leans or rolls outward due to centrifugal force. This tilting action is evident when using conventional “soft” springs. The hydrostatic system is “soft” during the movement of a single wheel, but if the two outer suspension units are loaded during cornering, a stiffening of the hydrostatic system occurs.
Under this type of load, there is no fluid movement from one unit to another. Instead, the increased pressure of the liquid deflects the rubber springs, which provide a marked resistance to the tilt of the body. During the rebound of the vehicle, all four wheels drift at the same time. To resist this movement, all hydrostatic units work in a similar way to how they react when rolling.
Hydra-gas Suspension System:
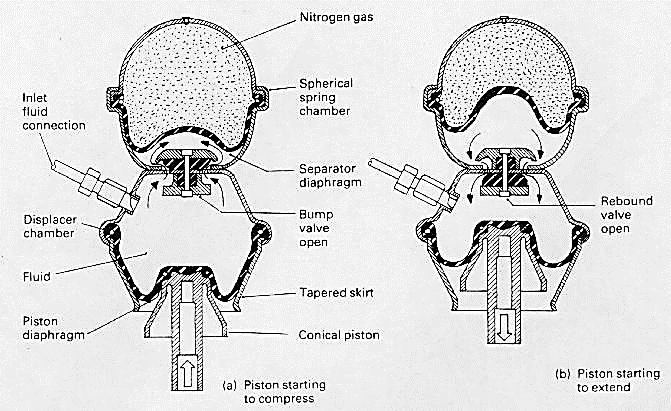
The spring unit consists of a nitrogen-filled spherical spring chamber welded to a double conical displacement chamber.
A hydraulic damper in the form of a pair of rubber compression blocks separates both the spherical spring and the displacement chambers, its function is to control the flow of fluid as it passes back and forth between the two chambers.
The displacer chamber is sealed at its lower end by a load-absorbing nylon reinforced rubber diaphragm (piston diaphragm) that rolls between the tapered piston and the tapered displacer chamber skirt as the suspension deflect toward up and down when the wheels pass over any unevenness in the road surface.
Inside the spherical chamber is a butyl rubber diaphragm (separator diaphragm) that separates the sphere into an upper region charged with nitrogen (17.5 bar) (the spring medium) which is sealed for life and the lower region which is filled with liquid.
Initially, the fluid is pumped into the displacer chamber until it reaches the nitrogen charging pressure. It will then compress and lift the separator diaphragm at the bottom of the ball.
Since the gas and fluid pressures are equal, the separator diaphragm is not subjected to heavy loads, in fact, it only works as a flexible wall to keep gas and fluid separate.
A water-based fluid containing 50% industrial alcohol and a small percentage of anti-corrosion additive is pumped into the system at a pressure of 23 bar with the car in the unloaded state, this being the condition in which the car body is the height from the ground is checked.
An advantage of using the rolling diaphragm type of displacer is that a water-based fluid can be used as opposed to oil that would not have such stable viscosity characteristics.
The effective area of the piston that compresses the fluid is the projected area of the displacer diaphragm that is not supported by the internal tapered skirt of the displacer chamber.
Therefore, as the load on the displacer piston increases, and the piston is pushed further into the chamber, less of the displacer diaphragm will be supported by the chamber skirt and more will be part of the projected effective area piston.
The consequence of the upward thrust of the diaphragm piston into the displacer chamber is that the piston loading area increases as the diaphragm moves away from its conical chamber support skirt.
As a result, the resistance offered by the fluid against the upward movement of the piston increases.
In other words, due to the tapered chamber skirt, the speed of the spring (stiffness) increases in proportion to the deflection of the spring.
The progressive action of the rubber valve between the two chambers provides a measure of damping that slows down bump and bounce movements caused by tire impact on bumpy roads.
Shock absorber:
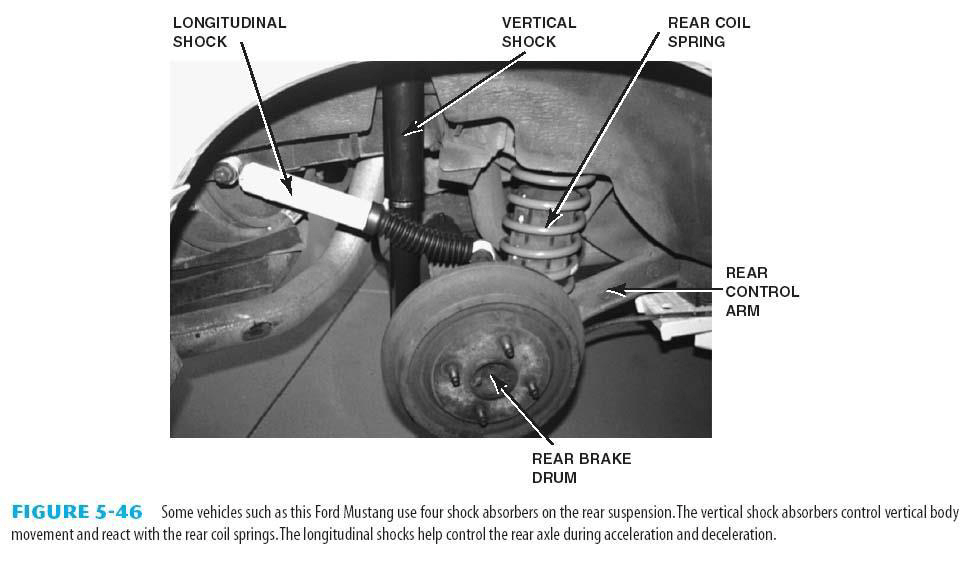
Shock absorbers are used in all conventional suspension systems to damp and control the movement of the vehicle’s springs. Without shock absorbers (shock absorbers), the vehicle would continue to bounce after hitting the potholes.
- The primary purpose of any shock or strut is to control ride and handling.
- Standard shock absorbers cannot support the weight of a vehicle.
- The springs support the weight of the vehicle; shock absorbers control the actions and reactions of the springs. Shock absorbers are also called shock absorbers.
- When a wheel rolls over a pothole, the wheel moves toward the body and compresses the springs of the vehicle.
- As the spring compresses, it stores energy. The spring then releases this stored energy, causing the vehicle body to rise (bounce).
When the shock is under compression:
- Fluid in-cylinder passes up through restricted piston valves
- At the same time, the fluid passes through a small valve in the cylinder tube.
- Due to this arrangement, the piston can move against the resistance of the fluid, whereby the impact is absorbed.
When the damper is under tension:
- The liquid from the top of the piston is pushed down through the piston valves.
- At the same time, the fluid enters through the valve at the bottom of the cylinder tube.
- The elongation of the shock absorber thus becomes very slow since it has to overcome the resistance of the fluid.
Active suspension:
An ideal suspension system should be able to perform numerous functions which are listed below;
1. Absorb the bumps and bounces imposed on the road suspension.
2. To control the degree of body roll when cornering.
3. Maintain body height and balance between light and full load conditions.
4. To prevent the body from diving and squatting when the car accelerates quickly or brakes
5. Provide a comfortable ride on rough roads while maintaining firm suspension for good steering response.
6. To isolate large and small round irregularities in the body both at high and low vehicle speed.
These demands of a conventional suspension are only partially met, as meeting one or more of the listed requirements may be contrary to meeting some of the other desired suspension properties.
For example, providing a soft spring for light loads will excessively reduce body height when the vehicle is fully loaded or, conversely, stiffening the spring to cope with heavy loads will produce a stiff suspension under light load conditions.
Consequently, it is possible that most conventional suspensions will only satisfy the essential requirements and will compromise some of the possibly less important considerations.
The active suspension will have incorporated design means to satisfy all the listed demands; however, even then, it may not be possible, due to design and cost limitations, to satisfy and overcome all of the inherent problems experienced with vehicle suspension.
Therefore, it would be justified to classify most suspensions that have some form of height levelling and body roll characteristics as semi-active suspensions only.
For an active suspension to function effectively, various sensors are installed around the vehicle to monitor changing driving conditions; the electrical signals provided by these sensors are continuously fed to the input of an electronic control unit.
The ECU evaluates and processes the data provided by the sensors on changes in speed, load and driving conditions imposed on the suspension system.
List of sensors that can be used in active suspensions:
1. Body height sensor
2. Steering wheel sensor
3. Longitudinal acceleration sensor
4. Lateral acceleration sensor
5. Brake pressure sensor
6. Brake pedal sensor
7. Accelerator pedal sensor
8. Load sensor
9. Vehicle speed sensor
10. Mode selector
An active suspension system has the ability to store, dissipate, and introduce energy into the system.
Its parameters may vary depending on operating conditions and may have different knowledge of prop deflection. The passive system is limited.
Types of Suspension System:
Active suspension
1. Electronically controlled hydraulic drive
2. Electromagnetic recuperator
Semi-active or adaptive suspension
1. Semi-active hydrocarbon suspension
2. Electronically controlled hydrocarbon suspension.
3. Electronically controlled air suspension
This publication has been extremely helpful. Thank you so much.