Table of Contents
Biogas generation plants
In Biogas generation plants a decentralized energy system, which can lead to self-sufficiency in thermal and energy needs and, at the same time, reduce environmental pollution. The main components of a modern biogas (or anaerobic digestion) plant include manure collection, anaerobic digester, effluent treatment, biogas storage and use of biogas/electricity generation equipment.
Before being fed into the gas grid, this raw biogas from the Biogas generation plants still needs to be processed in a processing plant to achieve natural gas quality, which means that substances such as carbon dioxide, hydrogen, oxygen, and sulfur are filtered. To do this, it is desulfurized by a filter material that contains iron, or its sulfur content is released by adding oxygen. In the final stage, the gas is dehumidified and can be used to generate electricity and heat, which is why many Biogas generation plants have cogeneration units.
The purified biogas
The purified biogas can also be fed into the gas network and transported to the points of consumption. A meter measures how much “green gas” has been fed. Thus, in addition to being conveyed to industrial customers, biogas can also be made available to bio-CNG dispensers at service stations for natural gas vehicles.
One of the main differentials of Biogas generation plants is their mode of operation. Depending on the substrate, the fermentation process is either wet or dry. For substrates such as manure with high liquid content, wet fermentation is always used. Dry or solid-state fermentation is used for stackable organic biomass such as municipal organic waste. A distinction can also be made between agricultural and industrial biogas generation plants. The input material is the deciding factor. Industrial biogas plants mainly use waste materials and residues, in accordance with the German “Biomass Waste Act (Bioabfallverordnung)”.
Biogas Factors in Biogas generation plants
Factors such as raw material availability and spatial distribution, soil and road conditions, specific biomass transport costs, storage costs, existing energy infrastructure, biomass seasonality issues, scale factors and the efficiency of conversion plants influence this optimization problem. The logistical aspects are particularly relevant in the use of raw materials with low energy density and high dispersion, as in the case of cattle manure.
In addition, small plants can facilitate the use of excess heat generated, which can meet local loads, if a cogeneration configuration is selected. Two generic analytical frameworks are proposed to calculate the optimal conversion plant size for biogas plants. A specific analysis of the influence of plant size on biogas and electricity production costs for maize Biogas generation plants for silage in the range 25-2000 kWe is proposed.
while the profitability of bovine manure Biogas generation plants with different sizes in Ontario are proposed In the cost of feed pipe fertilizer for beef and digested cattle from an AD plant as an alternative to truck transport is also explored, considering the influence of sludge concentrations and evaluating the minimum plant size for the profitability of piping systems.
The influence of plant size and biomass/digestive transport logistics on environmental performance is also addressed in the literature. The scale optimization problem is often related to the selection of the best location of plants in the territory, and for this purpose GIS-based tools are proposed for the evaluation of fertilizer potential. , logistical problems and for the identification of territorial agglomerates suitable for biogas and plant location.
Works of Biogas generation plants
Fresh organic waste is stored in a collection tank before its treatment in the homogenization tank which is equipped with a mixer to facilitate the homogenization of the waste stream. The uniformly mixed residues are passed through a macerator to obtain particles of uniform size of 5-10 mm and pumped into an anaerobic digester of adequate capacity, where the stabilization of the organic residues takes place.
In anaerobic digestion, organic material is converted into biogas by a series of groups of bacteria into methane and carbon dioxide. Most commercial digesters are full-mix and plug-flow reactors operating at mesophilic temperatures. The type of digester used varies according to the consistency and solids content of the raw material, the capital investment factors and the primary objective of digestion.
Biogas cleaning
Biogas generation plants contains a significant amount of hydrogen sulfide gas (H2S) which must be removed due to its highly corrosive nature. H2S removal takes place in a biological desulfurization unit where a limited amount of air is added to the biogas in the presence of specialized aerobic bacteria that oxidize H2S to elemental sulfur.
Biogas generation plants use Biogas is dried and fed from a cogeneration unit to a generator to produce electricity and heat. The size of the cogeneration plant depends on the amount of biogas produced daily.
Digestive treatment
The digested substrate is passed through screw presses for dehydration and then subjected to solar drying and conditioning to provide high-quality organic fertilizer. Press water is treated in an activated sludge effluent treatment plant consisting of an aeration tank and a secondary clarifier. Treated wastewater is recycled to meet the plant’s internal requirements.
Control system
Continuous monitoring of the biogas generation plants is carried out through a remote-control system such as the Supervisory Control and Data Acquisition (SCADA) system. This remote system facilitates immediate feedback and adjustments, which can translate into energy savings.
A Biogas generation plant is where biogas is produced from the fermentation of biomass. The substrate used to produce this methane-containing gas is usually made from energy crops such as corn or waste materials such as manure or food waste. The fermentation residue left over from the substrates at the end of the process can be used as fertilizer.
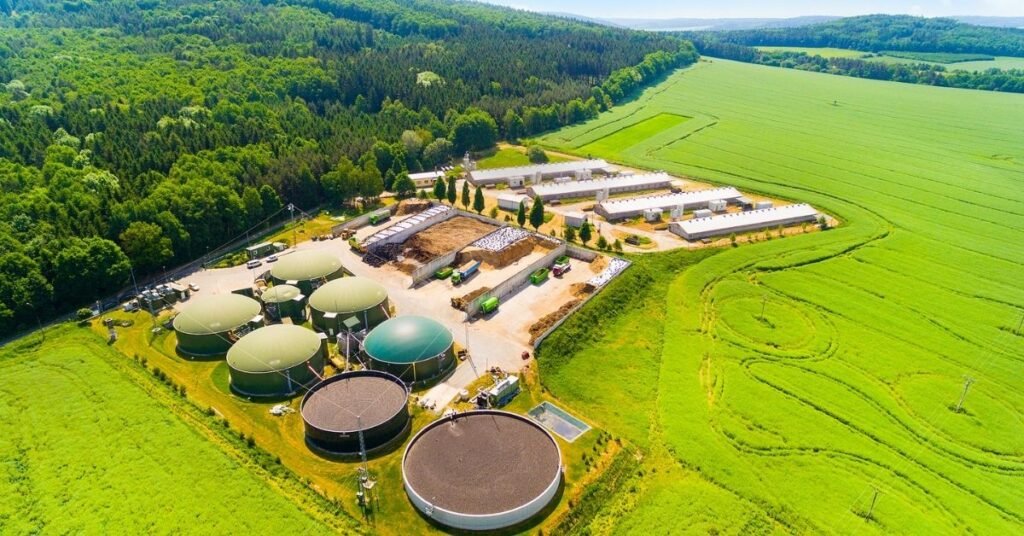
Biogas is produced by micro bacterial decomposition of the substrate in an oxygen-free environment, ie, under anaerobic conditions. To do this, the substrate is pumped into fermenters. The substrate is stored here under anaerobic conditions and is periodically moved by agitators to prevent surface foaming and sinking layers. This also allows the biogas to rise more easily. Unlike the decomposition of biomass under aerobic conditions (eg composting), under anaerobic conditions micro bacterial organisms can use only a small part of the energy contained. Anaerobic unusable energy is contained in the “waste product” of the biogas in the form of biomethane
(Engineeringhulk) is an amazing website