Table of Contents
3D reverse engineering is an exciting realm of study that transforms physical objects into digital representations. While the concept might seem futuristic to some, industries from automotive to entertainment have harnessed its capabilities for various applications.
Introduction to 3D Reverse Engineering
3D reverse engineering involves the process of capturing the physical dimensions and characteristics of an object and converting it into a digital 3D model. The digitized model can then be modified, analyzed, or integrated into other systems, depending on the user’s needs.
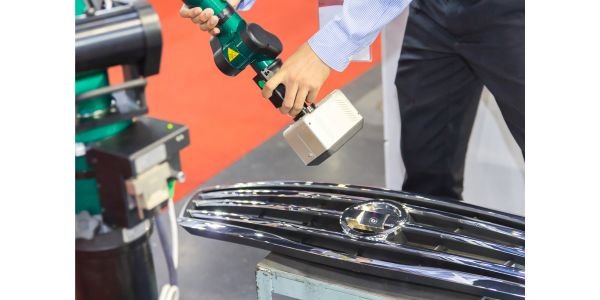
Process of 3D Reverse Engineering
Here’s a basic overview of the steps involved:
Data Acquisition
This involves capturing the geometrical shape and details of the object. The most common method is 3D scanning, which can be done using:
- Laser Scanners: These project a laser beam onto the object’s surface and capture its reflection to determine the shape and contours.
- Photogrammetry: This method involves capturing multiple images of the object from different angles and using them to derive a 3D model.
Point Cloud Generation
The raw data from 3D scanners usually takes the form of a ‘point cloud’— a large collection of points that represent the object’s surface.
Data Processing
The point cloud data is processed to remove noise, outliers, or any irrelevant data. This cleaned-up point cloud is then converted into a mesh, which is a more user-friendly representation comprising interconnected triangles or polygons.
CAD Model Generation
Using specialized software, the mesh can be converted into a more structured Computer-Aided Design (CAD) model. The CAD model can be parametric (having meaningful parameters and relations) or non-parametric, depending on the application.
Verification
Once the CAD model is generated, it’s crucial to verify its accuracy. This might involve comparing the digital model to the original object or ensuring it fits within the intended system.
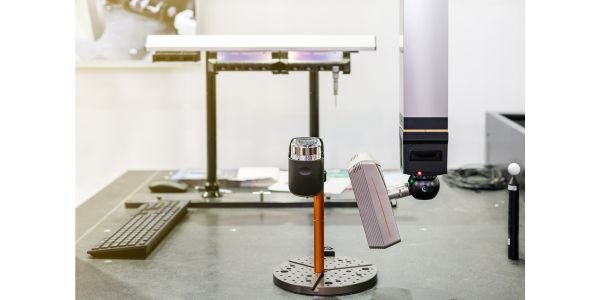
Applications of 3D Reverse Engineering
- Manufacturing and Industry: Manufacturers often use 3D reverse engineering when they need to recreate parts for which there are no existing blueprints, or when they aim to improve upon an existing design.
- Automotive: For retrofitting parts, redesigning components, or benchmarking competitor products.
- Aerospace: For creating replacement parts or integrating newer systems into older aircraft structures.
- Entertainment and Gaming: For digitizing real-world objects or locations to be used in video games or simulations.
- Archaeology and Heritage Preservation: To digitally preserve artifacts or historic sites.
Benefits
- Saves Time: Rather than designing from scratch, engineers can modify existing designs.
- Preservation: Delicate or rare items can be digitized and preserved in a digital format.
- Enhances Creativity: Designers can build upon existing designs, pushing the boundaries of what’s possible.
- Facilitates Customization: Tailoring products to specific needs becomes feasible.
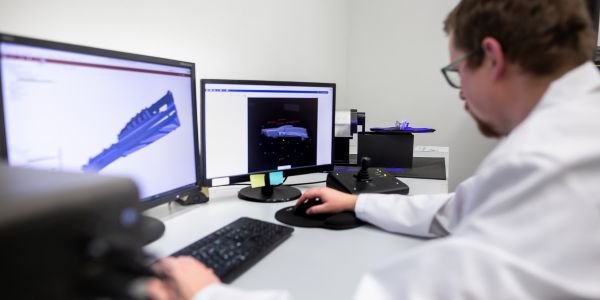
Challenges
- Data Accuracy: Ensuring the accuracy of scanned data is critical. Misinterpretations can lead to flawed models.
- Software Limitations: Not all software can handle large point clouds or generate accurate CAD models.
- Hardware Limitations: High-quality 3D scanners can be costly, and cheaper alternatives might not provide the necessary detail.
3D reverse engineering stands as a testament to the merging of the physical and digital worlds. Its transformative capabilities offer industries the means to innovate, preserve, and optimize in ways previously considered unattainable.
However, like any technology, it comes with its challenges. Successful implementation requires an understanding of both its capabilities and its limitations.
Also, read 3D Printing
Comment on “3D Reverse Engineering: A Deep Dive”
Comments are closed.